3 682 läst · 31 svar
4k läst
31 svar
Bill Pentzcyklon, byggtråd
Nästa steg var att göra mallar för att hålla alla delar runda. Jag använde 15 mm konstruktionsplywood, det funkade fint. Orkade inte göra en egen cirkelfräsjigg så jag köpte Festools som passar till fräsen.
Mallar görs till huvudcylindern/övre delen av konen (2 st), utloppsröret (2 st) och nedre delen av konen (och det som Bill kallar ”dust chute”), 2 st.
Fasade ena kanten så att de blir lättare att ta i och ur.
För utloppscylindern och ena mallen för huvudcylindern gjordes relativt stora hål i mitten, för att komma åt att arbeta inne i cyklonen vid montering. Den andra mallen för huvudcylindern ska sedan användas som lock, och utloppscylindern ska gå igenom den. Väntade därför med att göra det hålet tills den cylindern var färdig.
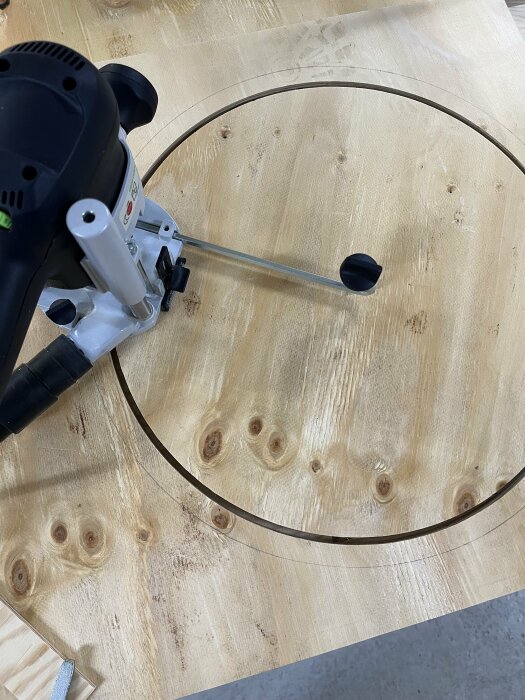
Inloggade ser högupplösta bilder
Logga in
Skapa konto
Gratis och tar endast 30 sekunder
Mallar görs till huvudcylindern/övre delen av konen (2 st), utloppsröret (2 st) och nedre delen av konen (och det som Bill kallar ”dust chute”), 2 st.
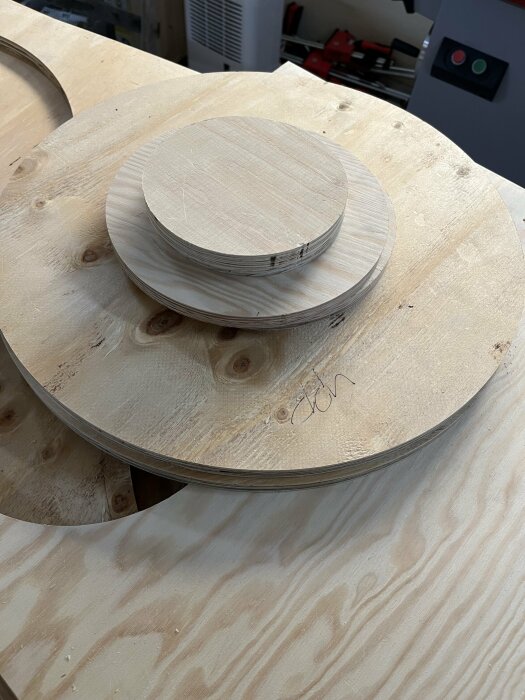
Inloggade ser högupplösta bilder
Logga in
Skapa konto
Gratis och tar endast 30 sekunder
Fasade ena kanten så att de blir lättare att ta i och ur.
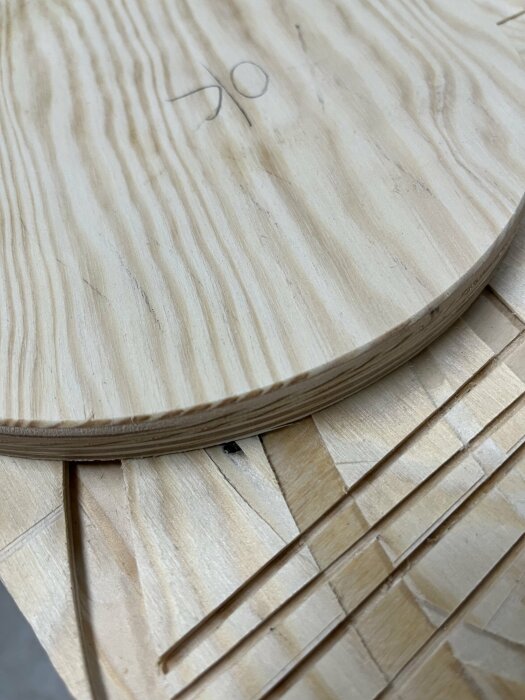
Inloggade ser högupplösta bilder
Logga in
Skapa konto
Gratis och tar endast 30 sekunder
För utloppscylindern och ena mallen för huvudcylindern gjordes relativt stora hål i mitten, för att komma åt att arbeta inne i cyklonen vid montering. Den andra mallen för huvudcylindern ska sedan användas som lock, och utloppscylindern ska gå igenom den. Väntade därför med att göra det hålet tills den cylindern var färdig.
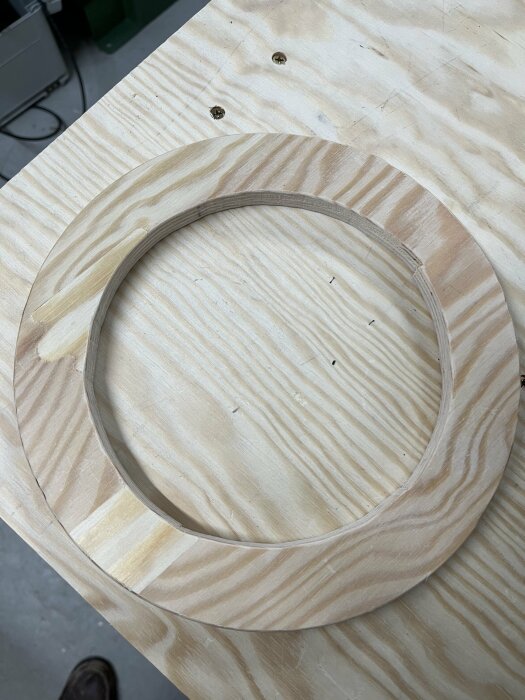
Inloggade ser högupplösta bilder
Logga in
Skapa konto
Gratis och tar endast 30 sekunder
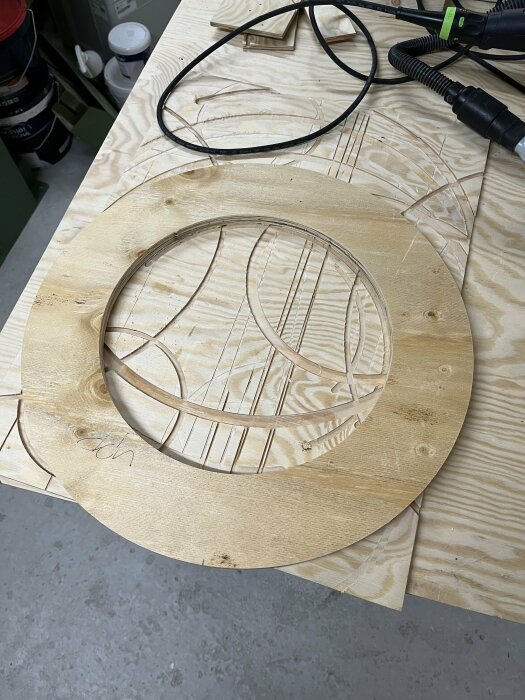
Inloggade ser högupplösta bilder
Logga in
Skapa konto
Gratis och tar endast 30 sekunder
Sammanfogning
Nu dags att börja sammanfoga de bockade och valsade delarna till sina slutliga former. Först ut är utloppscylindern. Flera ihopsatta slangklämmor används för att tvinga plåten runt plywoodmallarna.
En extra träkloss användes för att få halvorna att ligga an varandra. Befintliga borrhål i yttre halvan som överlappar den inre. Börja med hålet i mitten och borra igenom plåten under.
Popnita sedan inifrån och ut. För det estetiska vill man ha en popnit som sticker ut så lite som möjligt på utsidan, jag använde därför rostfria 3,2 x 4 mm popnitar. Man nitar inifrån ut för att få så slätt som möjligt på insidan, men svårt att få dem att sitta helt rakt ibland. Ett måste att ha en nittång med roterbart huvud då det blir trångt ibland, jag använde en Hazet 1963-2. Jobba sedan ett borrhål + nit i taget från mitten till ändarna, annars risk att det metallen skrynklar sig.
För att underlätta borrningen använde jag några reglar som tvingades fast i bordet.
Första borret gick av…
Köpte därför kortare borr med dubbla huvuden. Inga fler gick av!
Nöjd med resultatet.
Sedan kunde jag mäta exakt diameter på cylindern och fräsa hålet i plywoodlocket. Viktigt därför att centrummarkeringen från första fräsningen är kvar.
Nu dags att börja sammanfoga de bockade och valsade delarna till sina slutliga former. Först ut är utloppscylindern. Flera ihopsatta slangklämmor används för att tvinga plåten runt plywoodmallarna.
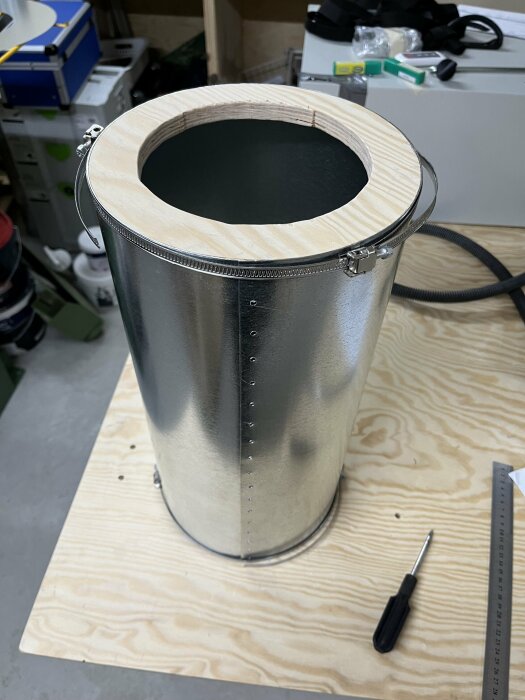
Inloggade ser högupplösta bilder
Logga in
Skapa konto
Gratis och tar endast 30 sekunder
En extra träkloss användes för att få halvorna att ligga an varandra. Befintliga borrhål i yttre halvan som överlappar den inre. Börja med hålet i mitten och borra igenom plåten under.
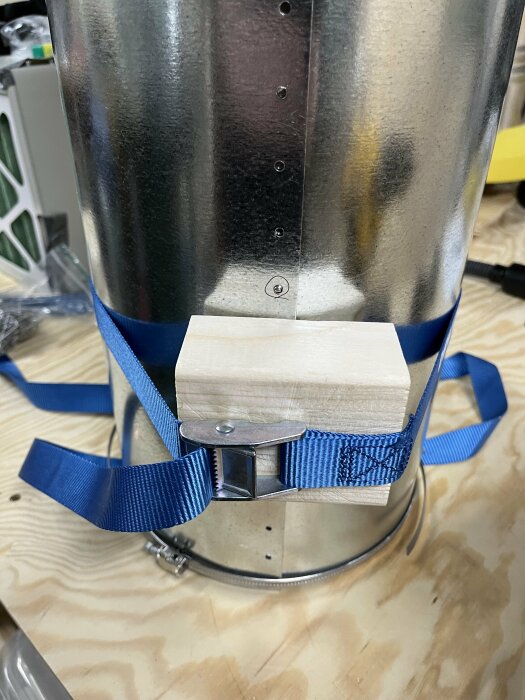
Inloggade ser högupplösta bilder
Logga in
Skapa konto
Gratis och tar endast 30 sekunder
Popnita sedan inifrån och ut. För det estetiska vill man ha en popnit som sticker ut så lite som möjligt på utsidan, jag använde därför rostfria 3,2 x 4 mm popnitar. Man nitar inifrån ut för att få så slätt som möjligt på insidan, men svårt att få dem att sitta helt rakt ibland. Ett måste att ha en nittång med roterbart huvud då det blir trångt ibland, jag använde en Hazet 1963-2. Jobba sedan ett borrhål + nit i taget från mitten till ändarna, annars risk att det metallen skrynklar sig.
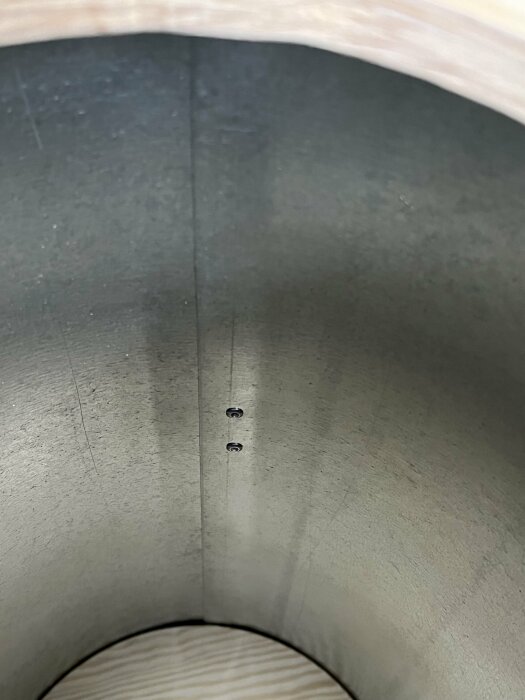
Inloggade ser högupplösta bilder
Logga in
Skapa konto
Gratis och tar endast 30 sekunder
För att underlätta borrningen använde jag några reglar som tvingades fast i bordet.
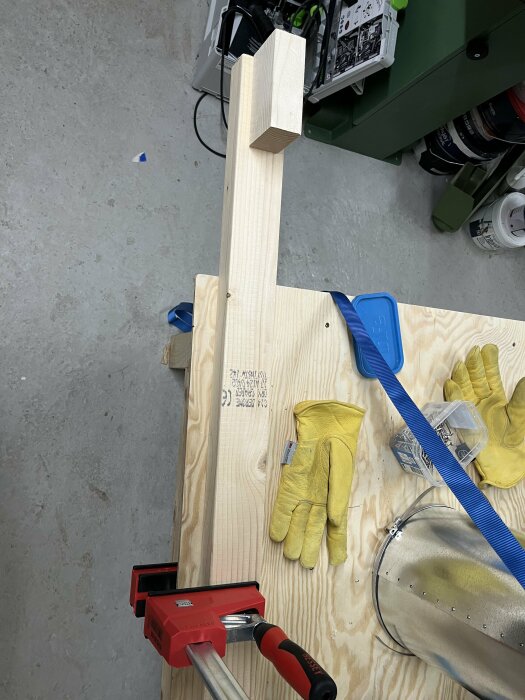
Inloggade ser högupplösta bilder
Logga in
Skapa konto
Gratis och tar endast 30 sekunder
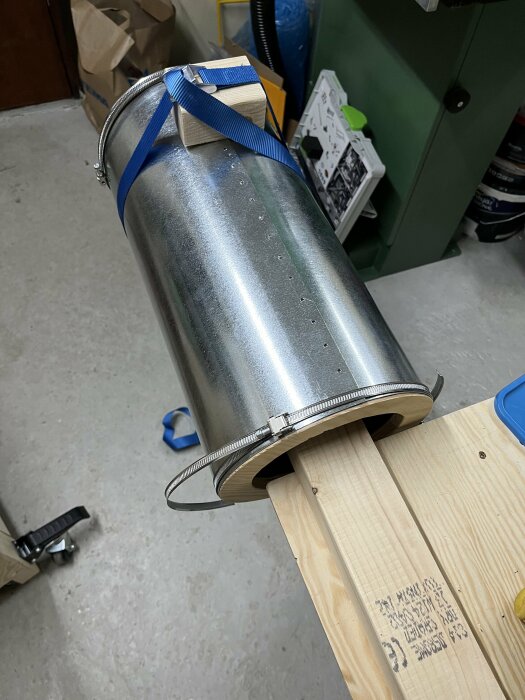
Inloggade ser högupplösta bilder
Logga in
Skapa konto
Gratis och tar endast 30 sekunder
Första borret gick av…
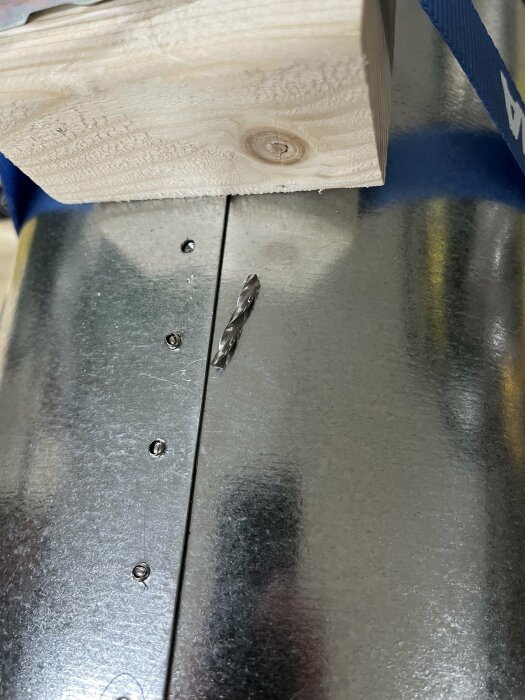
Inloggade ser högupplösta bilder
Logga in
Skapa konto
Gratis och tar endast 30 sekunder
Köpte därför kortare borr med dubbla huvuden. Inga fler gick av!
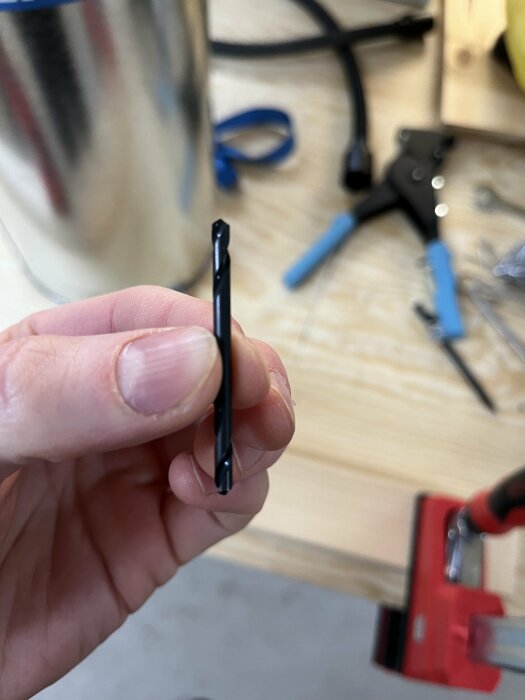
Inloggade ser högupplösta bilder
Logga in
Skapa konto
Gratis och tar endast 30 sekunder
Nöjd med resultatet.
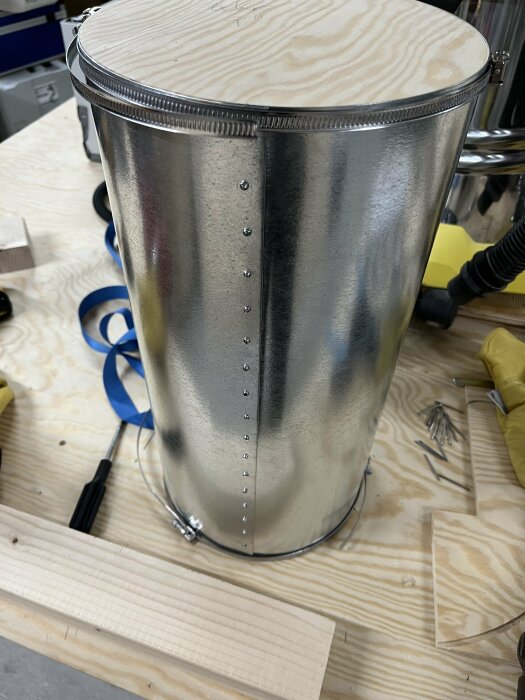
Inloggade ser högupplösta bilder
Logga in
Skapa konto
Gratis och tar endast 30 sekunder
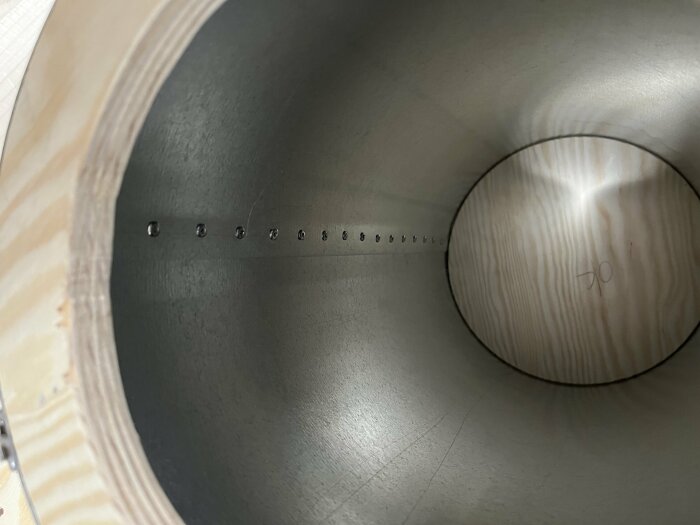
Inloggade ser högupplösta bilder
Logga in
Skapa konto
Gratis och tar endast 30 sekunder
Sedan kunde jag mäta exakt diameter på cylindern och fräsa hålet i plywoodlocket. Viktigt därför att centrummarkeringen från första fräsningen är kvar.
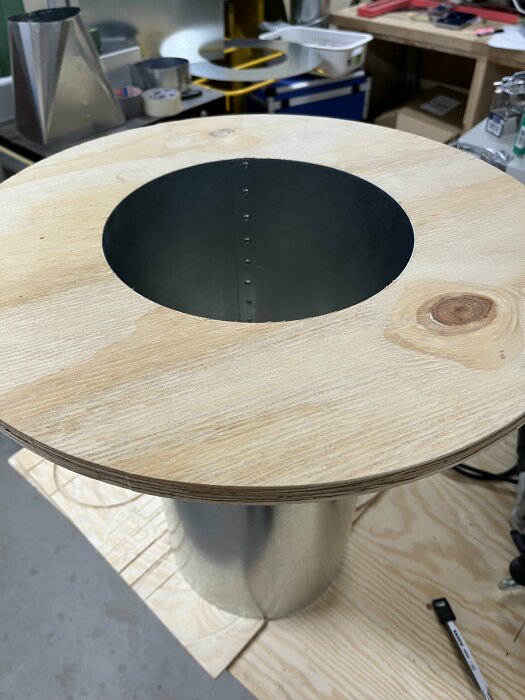
Inloggade ser högupplösta bilder
Logga in
Skapa konto
Gratis och tar endast 30 sekunder
Nu backar jag bandet lite. Innan jag sågade/fräste klart inre hålen på mallarna för huvudcylindern kollade jag så klart så att måtten på plåten stämde. Den gick inte ihop… saknades ca 6 mm.
Detta var väldigt störande med tanke på hur noggrann jag varit. Vet fortfarande inte var det blivit fel heller. Diametern på mallen var exakt 450 mm, omkretsen på plåten var rätt när jag mätte (räknade även vad diagonalen skulle vara och kontrollmätte den, den var samma och korrekt på båda sidor). Vet inte om det kan bero på hur metallen beter sig när man formar den, eller på att mitt måttband var kasst (skulle köpt en bra lång linjal!).
Men, hur gå vidare? Var inte sugen på att köpa ny plåt och börja om och kan inte lägga till mer plåt, beslutade därför att minska diametern på mallen tills cylindern gick ihop. En minskning av omkretsen med ca 6 mm innebär en minskning av diametern med ca 2 mm (eftersom omkrets = diametern * pi). Detta blir alltså en minskning av radien med ca 1 mm. Så det var bara att ställa in cirkeljiggen på att minska radien med 1 mm och fräsa om. Sen passade den bra, med vetskapen att jag kanske behöver fixa följdfel senare.
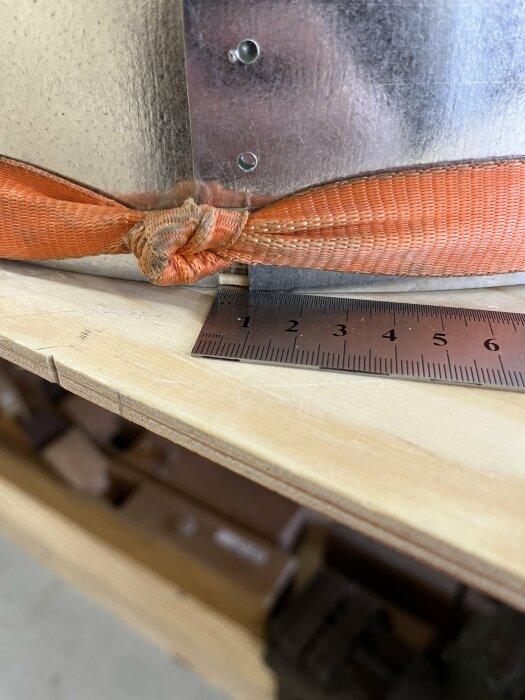
Inloggade ser högupplösta bilder
Logga in
Skapa konto
Gratis och tar endast 30 sekunder
Detta var väldigt störande med tanke på hur noggrann jag varit. Vet fortfarande inte var det blivit fel heller. Diametern på mallen var exakt 450 mm, omkretsen på plåten var rätt när jag mätte (räknade även vad diagonalen skulle vara och kontrollmätte den, den var samma och korrekt på båda sidor). Vet inte om det kan bero på hur metallen beter sig när man formar den, eller på att mitt måttband var kasst (skulle köpt en bra lång linjal!).
Men, hur gå vidare? Var inte sugen på att köpa ny plåt och börja om och kan inte lägga till mer plåt, beslutade därför att minska diametern på mallen tills cylindern gick ihop. En minskning av omkretsen med ca 6 mm innebär en minskning av diametern med ca 2 mm (eftersom omkrets = diametern * pi). Detta blir alltså en minskning av radien med ca 1 mm. Så det var bara att ställa in cirkeljiggen på att minska radien med 1 mm och fräsa om. Sen passade den bra, med vetskapen att jag kanske behöver fixa följdfel senare.
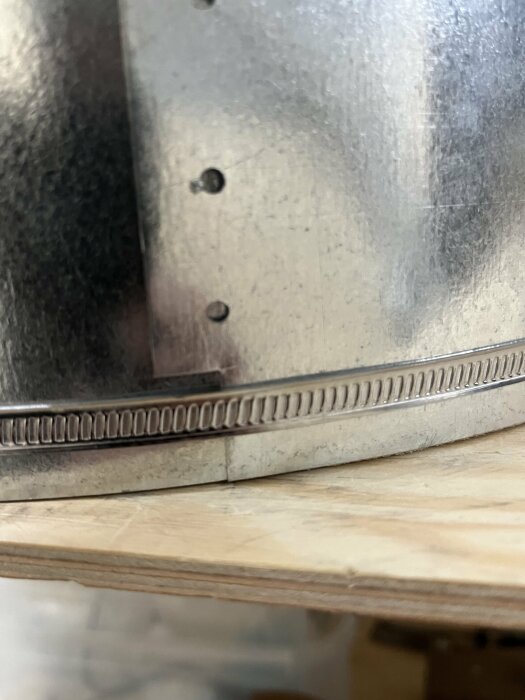
Inloggade ser högupplösta bilder
Logga in
Skapa konto
Gratis och tar endast 30 sekunder
Jag har inte sett på beräkningarna, men när man använder plåt så måste man komma ihåg att tjockleken på den har inverkan på dimensionering där toleranserna är små. Min gymnasielärare fick upprepa väldigt många gånger att material komprimeras på insidan radien och sträcks på utsidan. Så tumregeln han körde på var att ta bort (minst) 1 Tjocklek vid valsning. 25 år senare så minns jag tyvärr inte närmare än så. Kan vara ~65% material innanför radien och resterande utanför om jag är tvungen att gissa hej vilt. Hoppas någon mer verksam kan rätta mig om det är alldeles fel.
Tack för input! Det låter mycket rimligt. Tolkar jag dig rätt att tumregeln var att innerradien minskar med ca 1 materialtjocklek? Det stämmer i så fall väldigt bra med vad jag fick, använder 0,7 mm plåt och fick minska radien med 1 mm ca. Jag har inte tagit någon hänsyn till detta när jag klippt plåten, så längden på cylindern när jag klippt ut den (alltså omkretsen när den är valsad sedan) var 450 * pi = 1413,7 mm. Så om man ska kompensera för detta borde man göra den längre, ca: (450 + 2*materialtjocklek) * pi = 1418,1 mm? Har inte sett att Bill P skrivit om detta i hans bygginstruktioner men kan ha missat det.VidarH skrev:
Jag har inte sett på beräkningarna, men när man använder plåt så måste man komma ihåg att tjockleken på den har inverkan på dimensionering där toleranserna är små. Min gymnasielärare fick upprepa väldigt många gånger att material komprimeras på insidan radien och sträcks på utsidan. Så tumregeln han körde på var att ta bort (minst) 1 Tjocklek vid valsning. 25 år senare så minns jag tyvärr inte närmare än så. Kan vara ~65% material innanför radien och resterande utanför om jag är tvungen att gissa hej vilt. Hoppas någon mer verksam kan rätta mig om det är alldeles fel.
Väldigt förenklat, ett vanligt papper som man gör en modell/mall av är så tunn så det inverkar knappt då omkretsen på insidan och på utsidan är nästan densamma då ett vanligt papper är 0,08 till 0,1 mm tjockt. Men om man har en plåt på 1 mm så kommer omkretsen att diffa synligt. Diameter blir 99 mm på insidan och 101 mm på utsidan om man har en pappersmall för ett rör på 100 mm förutsatt att plåten formas kring centrum av materialet. (vilket det sällan gör och det finns tabeller och formler för olika legeringar) Så beroende på om det ska vara 100 mm innermått eller yttermått så får man lägga till eller ta bort en tjocklek. Knowledge is cool!
Redigerat:
Tack, är med på konceptet men undrade mest om det var radien eller diametern man skulle lägga till en materialtjocklek på. 🙂 Men då är det diametern, då förklarar det förmodligen inte hela min avvikelse. Antar att det även komprimeras mer ju mindre diameter man har.VidarH skrev:
Väldigt förenklat, ett vanligt papper som man gör en modell/mall av är så tunn så det inverkar knappt då omkretsen på insidan och på utsidan är nästan densamma då ett vanligt papper är 0,08 till 0,1 mm tjockt. Men om man har en plåt på 1 mm så kommer omkretsen att diffa synligt. Diameter blir 99 mm på insidan och 101 mm på utsidan om man har en pappersmall för ett rör på 100 mm förutsatt att plåten formas kring centrum av materialet. (vilket det sällan gör och det finns tabeller och formler för olika legeringar) Så beroende på om det ska vara 100 mm innermått eller yttermått så får man lägga till eller ta bort en tjocklek. Knowledge is cool!
Dags att arbeta vidare med konen. Började med att klippa flärparna i topp och botten.
Sedan popnita ihop den med samma metod som tidigare, från mitten och ut. Använde plywoodmallarna för att hålla den rund. För nederdelen byggde jag på mallen så att jag kunde ha en träbit tvärs över hålet, så att mallen hålls på plats trots konformen. Använde även basen på ett magnetstativ för att hålla ihop bitarna, hjälpte lite i alla fall.
Blev bra!
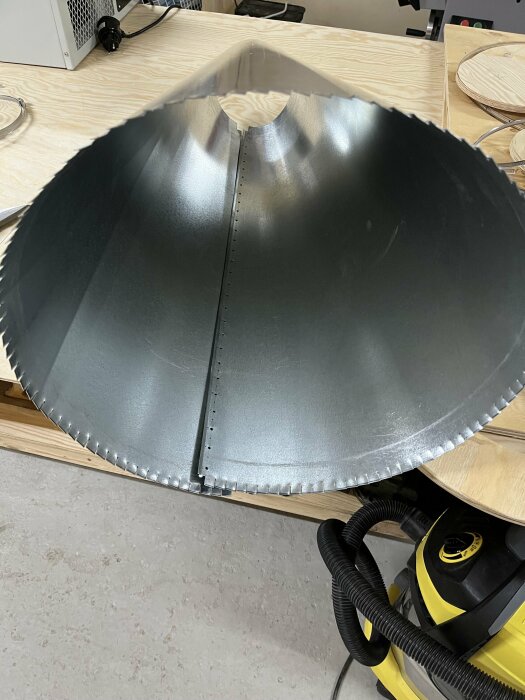
Inloggade ser högupplösta bilder
Logga in
Skapa konto
Gratis och tar endast 30 sekunder
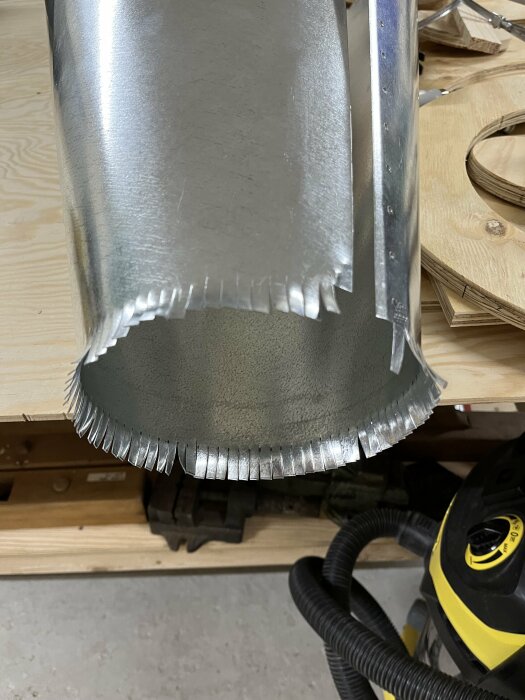
Inloggade ser högupplösta bilder
Logga in
Skapa konto
Gratis och tar endast 30 sekunder
Sedan popnita ihop den med samma metod som tidigare, från mitten och ut. Använde plywoodmallarna för att hålla den rund. För nederdelen byggde jag på mallen så att jag kunde ha en träbit tvärs över hålet, så att mallen hålls på plats trots konformen. Använde även basen på ett magnetstativ för att hålla ihop bitarna, hjälpte lite i alla fall.
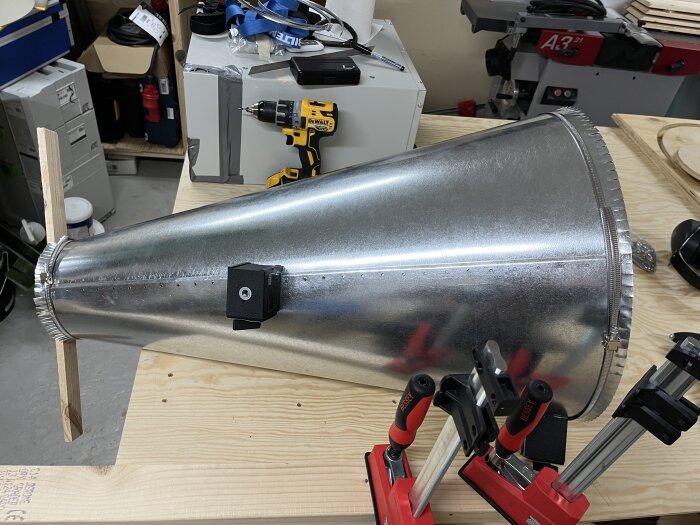
Inloggade ser högupplösta bilder
Logga in
Skapa konto
Gratis och tar endast 30 sekunder
Blev bra!
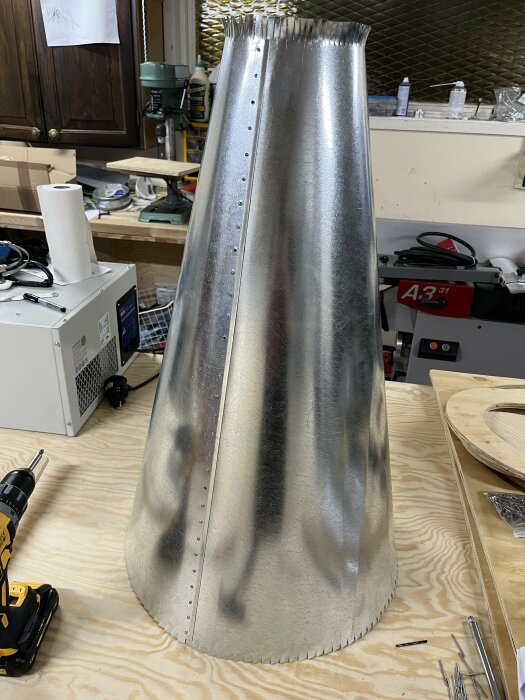
Inloggade ser högupplösta bilder
Logga in
Skapa konto
Gratis och tar endast 30 sekunder
För att vika flärparna lika mycket använde jag en bit plywood som jag gjort ett spår i med bandsågen. Sedan finjustera med en tång.
Var lite för snabb och gjorde både för övre och undre delen på konen. Undre skulle jag dock göra på annat sätt, så jag fick vika tillbaka dem senare.

Inloggade ser högupplösta bilder
Logga in
Skapa konto
Gratis och tar endast 30 sekunder
Var lite för snabb och gjorde både för övre och undre delen på konen. Undre skulle jag dock göra på annat sätt, så jag fick vika tillbaka dem senare.
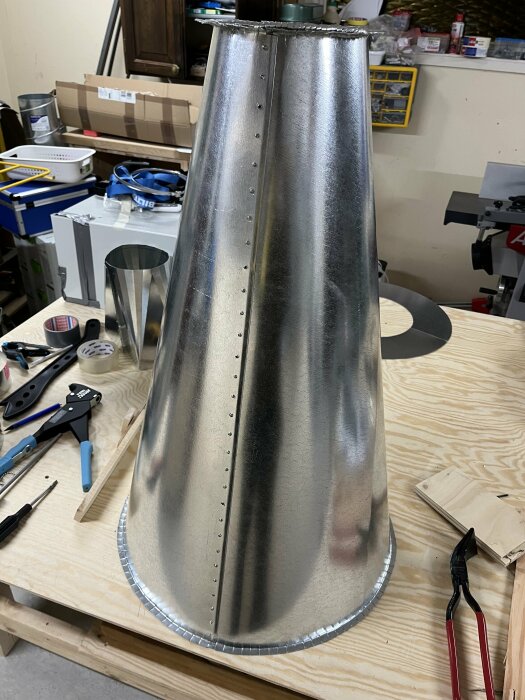
Inloggade ser högupplösta bilder
Logga in
Skapa konto
Gratis och tar endast 30 sekunder
Huvudcylindern gjordes på samma sätt.
Blev bra, dock insåg jag att jag gjort lite för många borrhål för fäste av inloppskanalen.
Sen klippa flärparna där inloppskanalen ska in.
Popnitade ihop inloppskanalen på samma sätt.
Sedan testa så att den passar.
Fick justera flärparna lite tills kanalen gick in och sidan linjerade med sömmen på cylindern.
Fixade sedan flärparna på nederdelen av huvudcylindern där den ska fästas mot konen.
Efter det borrade jag nya bättre hål för att fästa inloppet och popnitade fast den. Nu började det bli rätt så krångligt att popnita från insidan.
Slutligen använda en hammare för att banka tillbaka flärparna så att de sluter så tätt som möjligt.
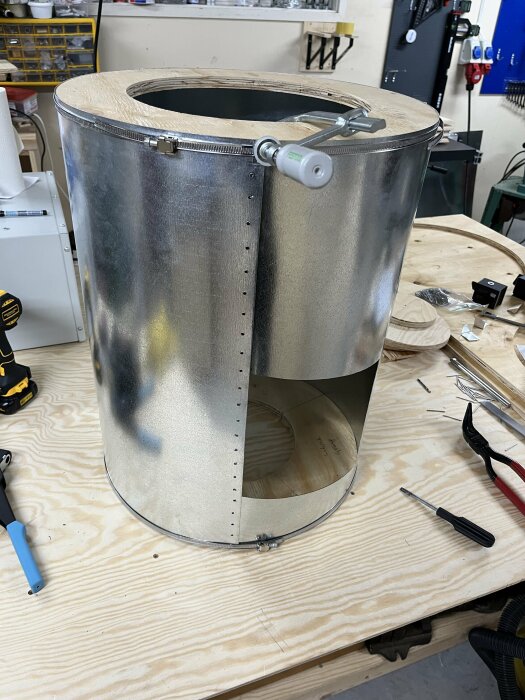
Inloggade ser högupplösta bilder
Logga in
Skapa konto
Gratis och tar endast 30 sekunder
Blev bra, dock insåg jag att jag gjort lite för många borrhål för fäste av inloppskanalen.
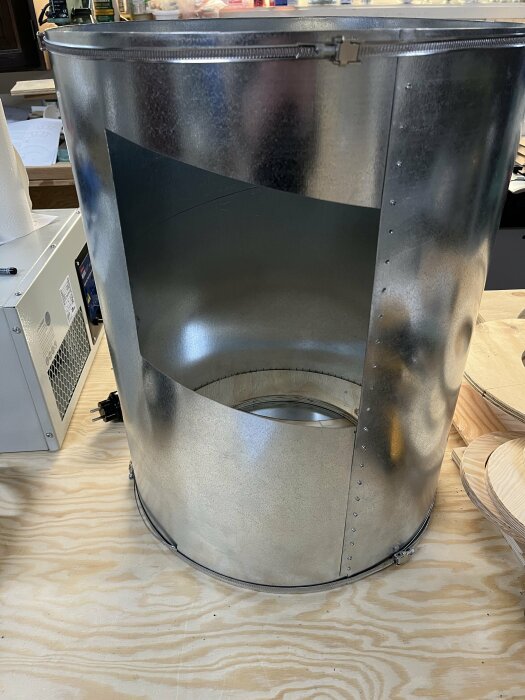
Inloggade ser högupplösta bilder
Logga in
Skapa konto
Gratis och tar endast 30 sekunder
Sen klippa flärparna där inloppskanalen ska in.
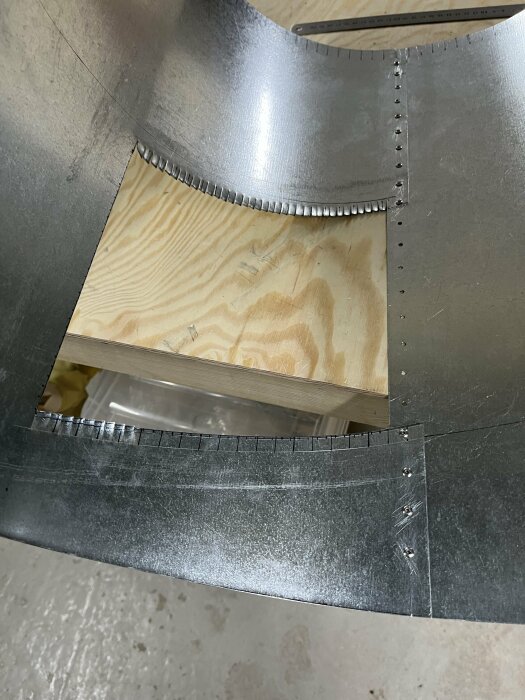
Inloggade ser högupplösta bilder
Logga in
Skapa konto
Gratis och tar endast 30 sekunder
Popnitade ihop inloppskanalen på samma sätt.
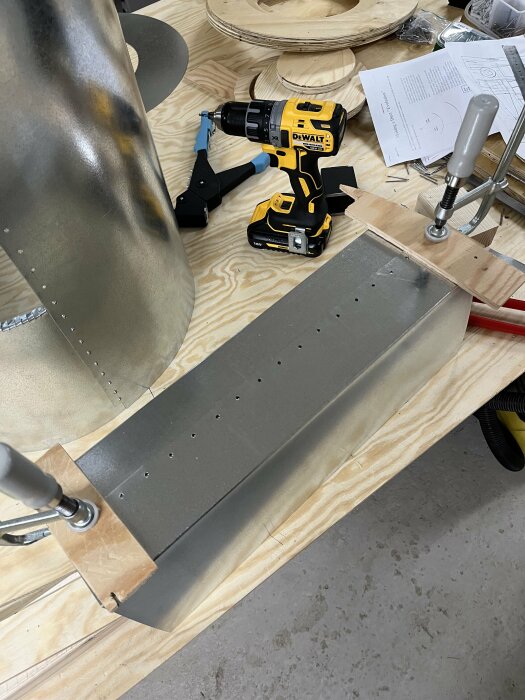
Inloggade ser högupplösta bilder
Logga in
Skapa konto
Gratis och tar endast 30 sekunder
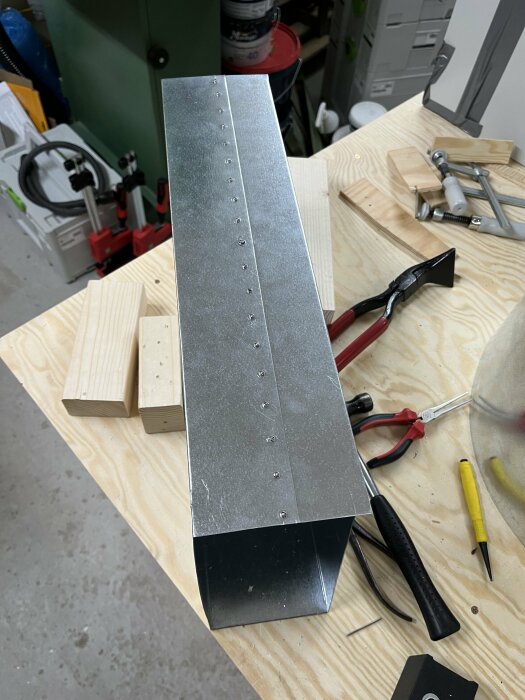
Inloggade ser högupplösta bilder
Logga in
Skapa konto
Gratis och tar endast 30 sekunder
Sedan testa så att den passar.
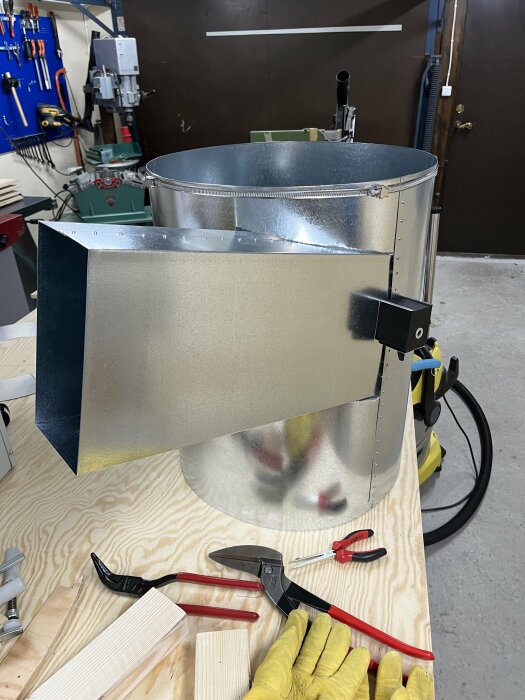
Inloggade ser högupplösta bilder
Logga in
Skapa konto
Gratis och tar endast 30 sekunder
Fick justera flärparna lite tills kanalen gick in och sidan linjerade med sömmen på cylindern.
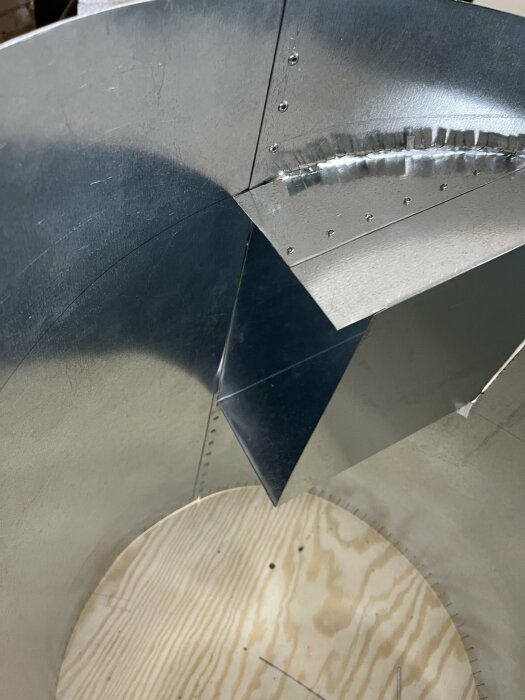
Inloggade ser högupplösta bilder
Logga in
Skapa konto
Gratis och tar endast 30 sekunder
Fixade sedan flärparna på nederdelen av huvudcylindern där den ska fästas mot konen.
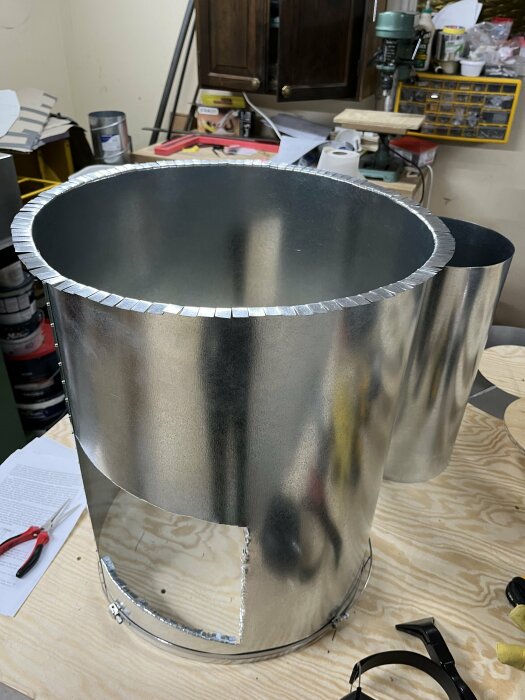
Inloggade ser högupplösta bilder
Logga in
Skapa konto
Gratis och tar endast 30 sekunder
Efter det borrade jag nya bättre hål för att fästa inloppet och popnitade fast den. Nu började det bli rätt så krångligt att popnita från insidan.
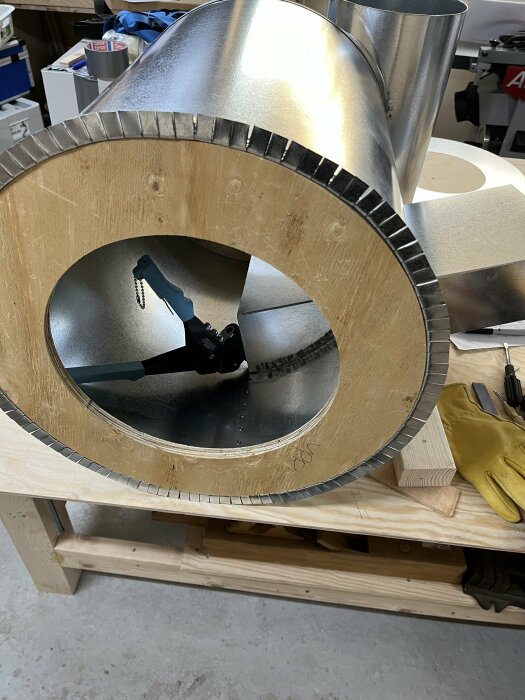
Inloggade ser högupplösta bilder
Logga in
Skapa konto
Gratis och tar endast 30 sekunder
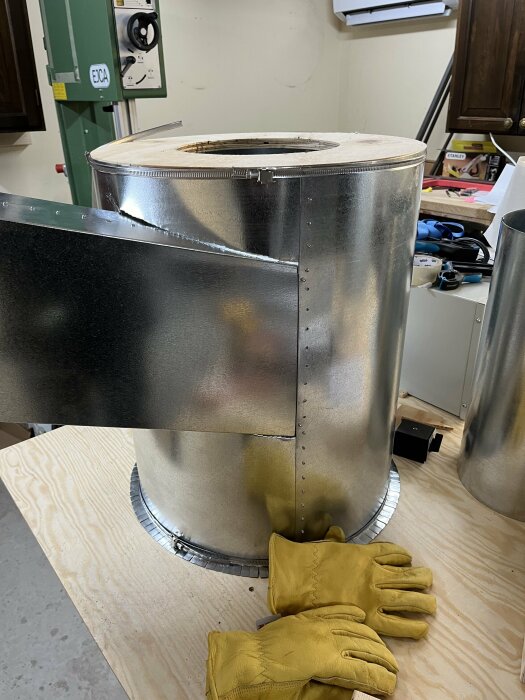
Inloggade ser högupplösta bilder
Logga in
Skapa konto
Gratis och tar endast 30 sekunder
Slutligen använda en hammare för att banka tillbaka flärparna så att de sluter så tätt som möjligt.
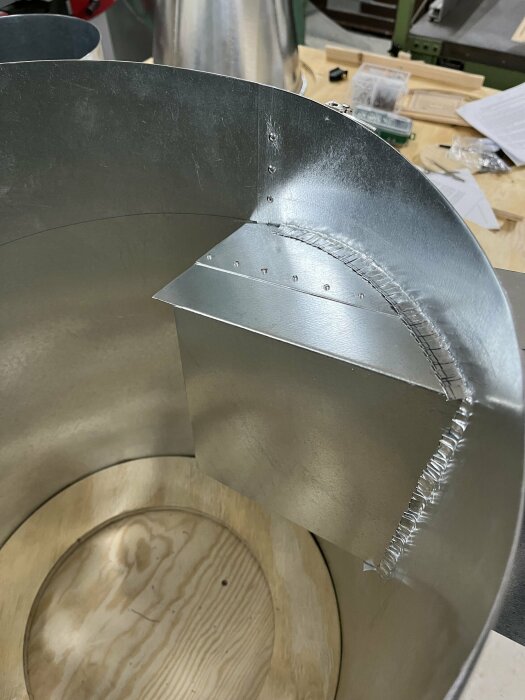
Inloggade ser högupplösta bilder
Logga in
Skapa konto
Gratis och tar endast 30 sekunder
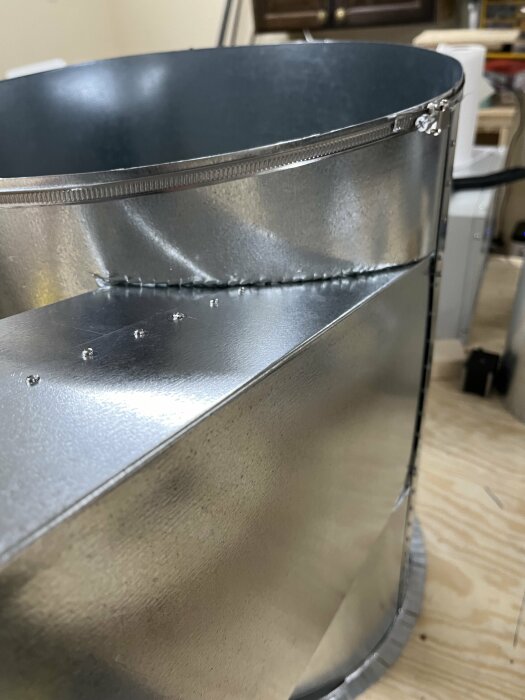
Inloggade ser högupplösta bilder
Logga in
Skapa konto
Gratis och tar endast 30 sekunder
Täta
Tätade alla skarvar och popnitar med MS-polymer (Tec7). Svårt att få bra jämn täckning över popnitarna. Inte helt nöjd med detta och hoppas att det inte påverkar funktionen allt för mycket. Bill rekommenderar att man lägger limmet på ena sidan skarven i samband med att man popnitar ihop, vilket nog blir bättre än om man gör det i efterhand som jag. Men vågade inte lägga på limmet innan jag nitat då det blir svårare att hålla allt linjerat samt riskerar att limmet härdar medans plåten inte ligger rätt. Till sist på med aluminiumtejp över skarven för att släta ut.
Prova passform för luftrampen
Inte helt lätt att få denna på plats, men den satt bra. Använde en klämma för att hålla den på plats mot övre delen av inloppet, sedan hålla den längs med ytterväggen och trycka upp den på undersidan av inloppet. Blev inte så stor glapp vid ytterväggarna. Fäste den dock inte ännu, ville ha kvar plywoodmall i när jag fäste konen. Eftersom diametern på cylinern var mindre än tänkt från början så gjorde jag en ny ramp anpassat för en mindre diameter (men med samma diameter på utloppet i mitten).
Sammanfoga cylindern och konen
Satte i plywoodmallarna i cylindern, testade var jag behöver vika upp flärparna för att kondelen skulle passa och markerade detta.
Sedan byggde jag en ny mall i plywood, denna anpassad för att vara på utsidan av cyklonen. Denna plus en likadan blir senare använd för upphängning. Nu används den för att hålla konen rund.
Böjde upp flärparna på cylindern med en tång och placerade sedan konen i.
Använde sedan en hammare för att böja över flärparna lite lätt, sedan knipa åt dem med tången. Inga problem att ta ut plywoodmallarna efteråt.
Tätade alla skarvar och popnitar med MS-polymer (Tec7). Svårt att få bra jämn täckning över popnitarna. Inte helt nöjd med detta och hoppas att det inte påverkar funktionen allt för mycket. Bill rekommenderar att man lägger limmet på ena sidan skarven i samband med att man popnitar ihop, vilket nog blir bättre än om man gör det i efterhand som jag. Men vågade inte lägga på limmet innan jag nitat då det blir svårare att hålla allt linjerat samt riskerar att limmet härdar medans plåten inte ligger rätt. Till sist på med aluminiumtejp över skarven för att släta ut.
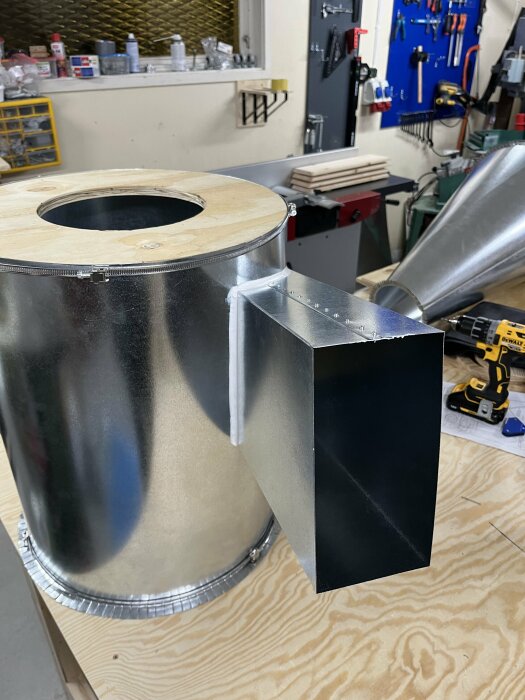
Inloggade ser högupplösta bilder
Logga in
Skapa konto
Gratis och tar endast 30 sekunder
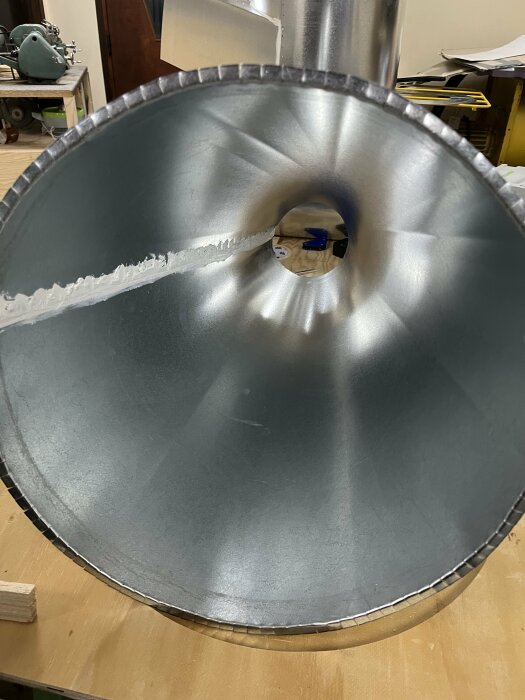
Inloggade ser högupplösta bilder
Logga in
Skapa konto
Gratis och tar endast 30 sekunder
Prova passform för luftrampen
Inte helt lätt att få denna på plats, men den satt bra. Använde en klämma för att hålla den på plats mot övre delen av inloppet, sedan hålla den längs med ytterväggen och trycka upp den på undersidan av inloppet. Blev inte så stor glapp vid ytterväggarna. Fäste den dock inte ännu, ville ha kvar plywoodmall i när jag fäste konen. Eftersom diametern på cylinern var mindre än tänkt från början så gjorde jag en ny ramp anpassat för en mindre diameter (men med samma diameter på utloppet i mitten).
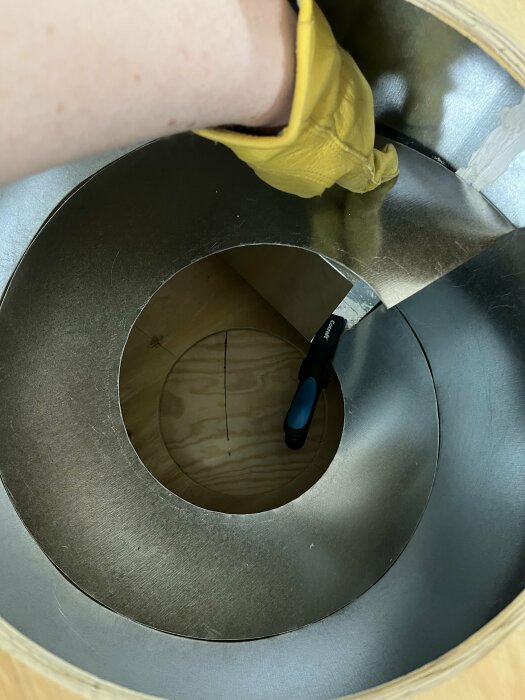
Inloggade ser högupplösta bilder
Logga in
Skapa konto
Gratis och tar endast 30 sekunder
Sammanfoga cylindern och konen
Satte i plywoodmallarna i cylindern, testade var jag behöver vika upp flärparna för att kondelen skulle passa och markerade detta.
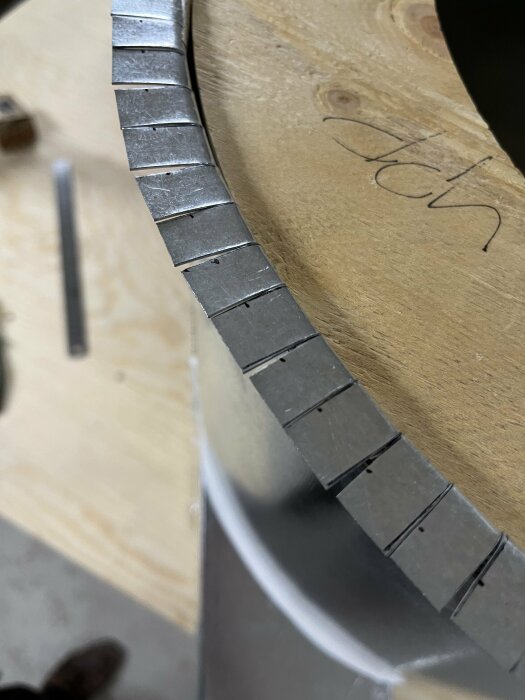
Inloggade ser högupplösta bilder
Logga in
Skapa konto
Gratis och tar endast 30 sekunder
Sedan byggde jag en ny mall i plywood, denna anpassad för att vara på utsidan av cyklonen. Denna plus en likadan blir senare använd för upphängning. Nu används den för att hålla konen rund.
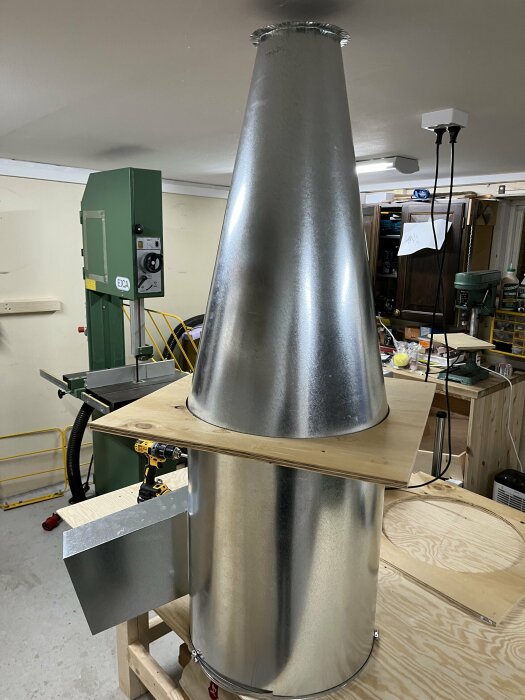
Inloggade ser högupplösta bilder
Logga in
Skapa konto
Gratis och tar endast 30 sekunder
Böjde upp flärparna på cylindern med en tång och placerade sedan konen i.
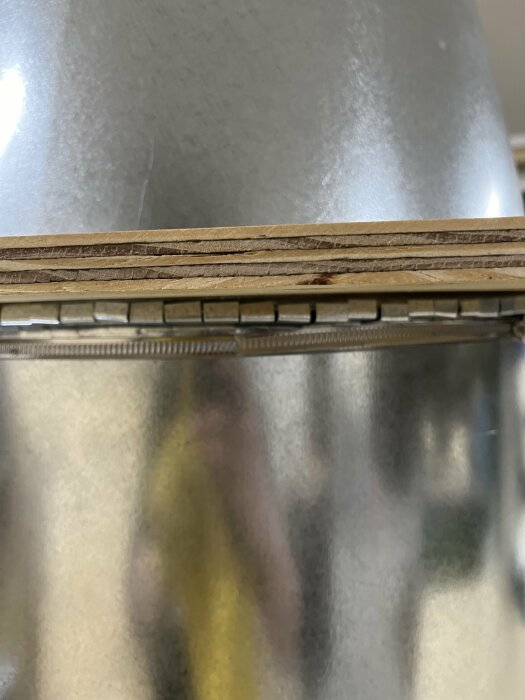
Inloggade ser högupplösta bilder
Logga in
Skapa konto
Gratis och tar endast 30 sekunder
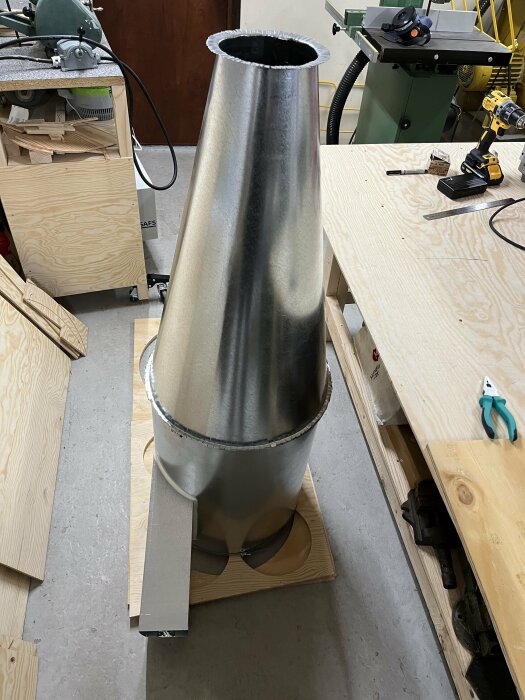
Inloggade ser högupplösta bilder
Logga in
Skapa konto
Gratis och tar endast 30 sekunder
Använde sedan en hammare för att böja över flärparna lite lätt, sedan knipa åt dem med tången. Inga problem att ta ut plywoodmallarna efteråt.
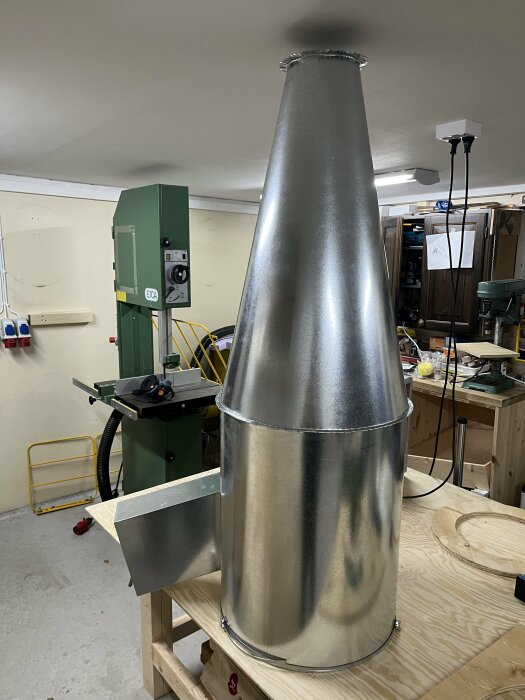
Inloggade ser högupplösta bilder
Logga in
Skapa konto
Gratis och tar endast 30 sekunder
Produkter som diskuteras: "aluminiumtejp"

Aluminiumtejp
Aluminiumtejp är en robust och flexibel lösning för olika projekt. Den är idealisk för att fästa, reparera och försegla metallytor och värmekänslig elektronik. Den är också vädertålig, vilket gör den lämplig för både inomhus- och
Läs mer
Fästa rampen
Rampen fästes först i överkant med en popnit på översidan av inloppet. Borrade först hål i rampen, spände sedan fast den där den ska sitta och borrade igenom inloppet.
Sedan samma sak med undre delen. Den undre delen var väldigt svår att både borra och fästa när man bara har åtkomst från ovansidan. Blev inte riktigt lika bra som när jag testade hur den passade tidigare, men rätt så bra ändå. Det underlättade att ha de utvändiga plywoodmallarna på så att den kunde stå på dessa.
Sedan täta runtom rampen, det behövs endast på ytterkanterna (inte in mot mitten vid utloppscylindern). Använde även Tec7 för att limma fast en 1 mm gummiduk precis vid inloppet (det Bill kallar ”blast sheet”) för att minska slitage på plåten där. Hittade en duk på Bauhaus jag kunde använda för detta och köpa en liten bit av (https://www.bauhaus.se/gummimatta-firestone-30-5m-x-6-1m-x-1mm-pris-m). Den är svart så lite svår att se på bilden.
Nitade fast och tätade spånutloppet (dust chute). Fuskade lite och satte flärparna från konen på utsidan istället för insidan här då det passade bättre. Blir inte så mycket kant som spån kan samlas på ändå.
Rampen fästes först i överkant med en popnit på översidan av inloppet. Borrade först hål i rampen, spände sedan fast den där den ska sitta och borrade igenom inloppet.
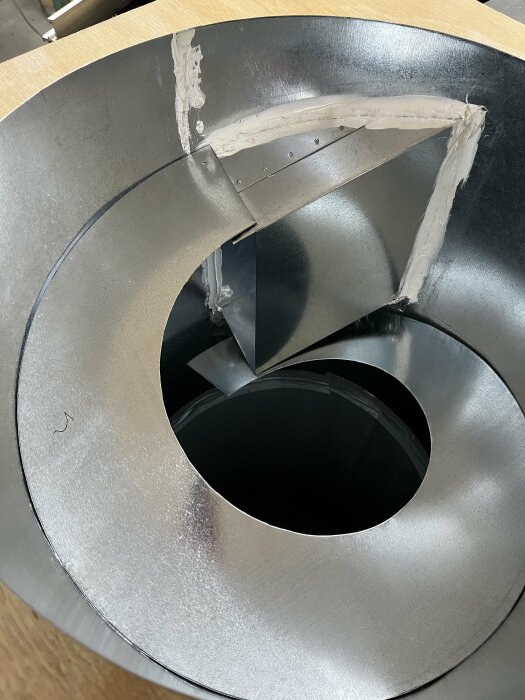
Inloggade ser högupplösta bilder
Logga in
Skapa konto
Gratis och tar endast 30 sekunder
Sedan samma sak med undre delen. Den undre delen var väldigt svår att både borra och fästa när man bara har åtkomst från ovansidan. Blev inte riktigt lika bra som när jag testade hur den passade tidigare, men rätt så bra ändå. Det underlättade att ha de utvändiga plywoodmallarna på så att den kunde stå på dessa.
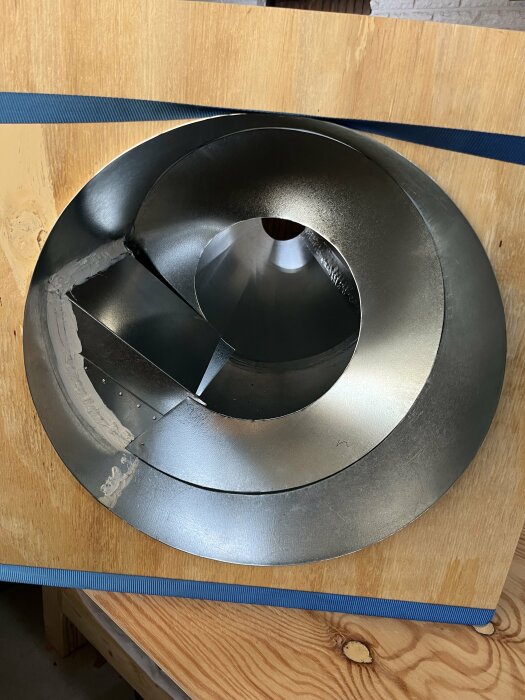
Inloggade ser högupplösta bilder
Logga in
Skapa konto
Gratis och tar endast 30 sekunder
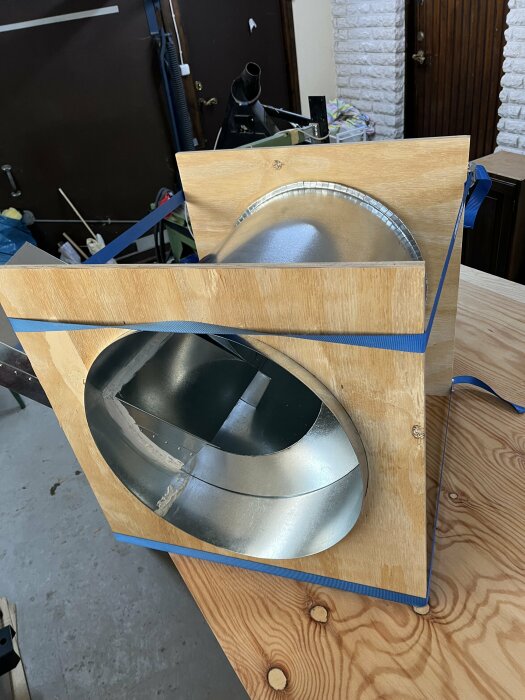
Inloggade ser högupplösta bilder
Logga in
Skapa konto
Gratis och tar endast 30 sekunder
Sedan täta runtom rampen, det behövs endast på ytterkanterna (inte in mot mitten vid utloppscylindern). Använde även Tec7 för att limma fast en 1 mm gummiduk precis vid inloppet (det Bill kallar ”blast sheet”) för att minska slitage på plåten där. Hittade en duk på Bauhaus jag kunde använda för detta och köpa en liten bit av (https://www.bauhaus.se/gummimatta-firestone-30-5m-x-6-1m-x-1mm-pris-m). Den är svart så lite svår att se på bilden.
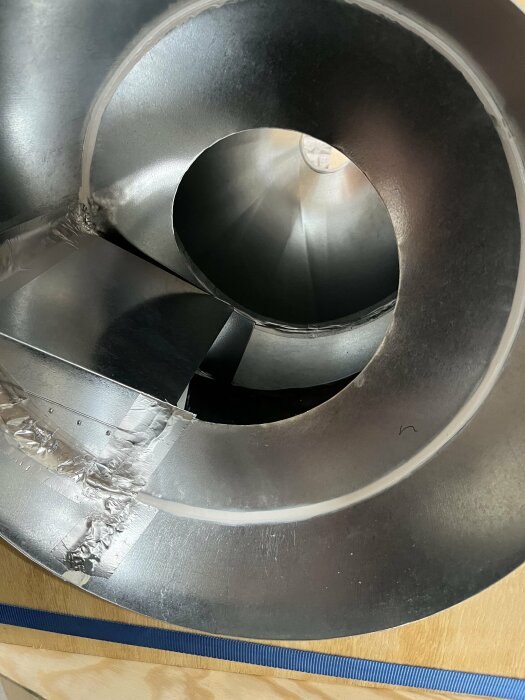
Inloggade ser högupplösta bilder
Logga in
Skapa konto
Gratis och tar endast 30 sekunder
Nitade fast och tätade spånutloppet (dust chute). Fuskade lite och satte flärparna från konen på utsidan istället för insidan här då det passade bättre. Blir inte så mycket kant som spån kan samlas på ändå.
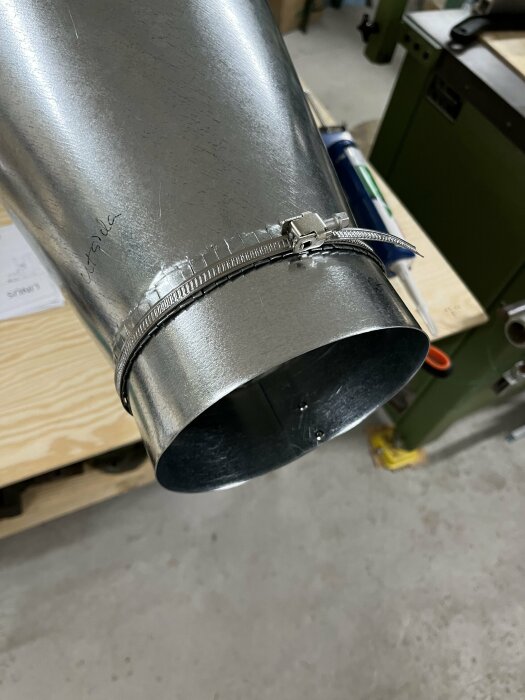
Inloggade ser högupplösta bilder
Logga in
Skapa konto
Gratis och tar endast 30 sekunder
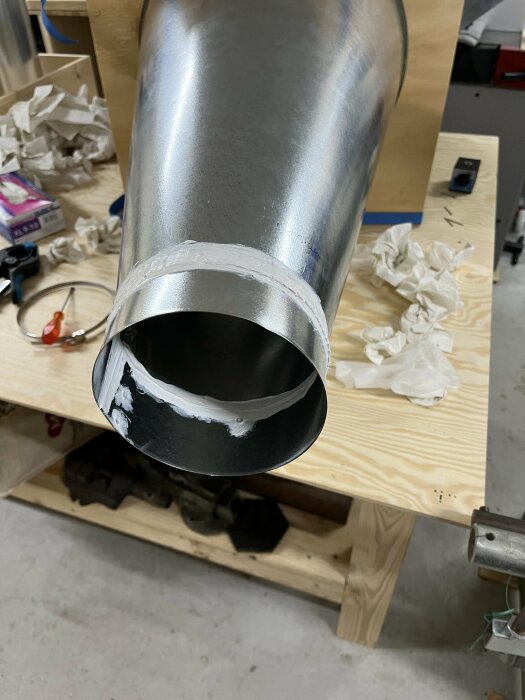
Inloggade ser högupplösta bilder
Logga in
Skapa konto
Gratis och tar endast 30 sekunder
Testade så att övergången passade till inloppet, funkade fint.
Sedan popnita fast och täta. Har just nu en spironippel på.
Skruvade fast utloppsröret i plywoodlocket och plywoodlocket i cykloncylindern. Utloppscylindern tog emot lite inloppet, så möjligen skulle jag gjort utloppet någon mm mindre efter att diametern på huvudcylindern blev mindre.
Byggde ihop plywooden med några reglar för att kunna hänga upp den. Använde rejäla vinkelbeslag och väggkrokar för att hänga upp den. Eftersom jag endast har 2,10 m i takhöjd behöver jag sätta den vinklad. Finns en diskussion på Fine woodworking forum (tror jag att det var) där de diskuterar detta, Bill ska ha testat detta och det funkar bra så länge man har ca 30 graders lutning på konen så att större bitar glider ned.
Filter
Som filter har jag köpt två st patronfilter (Donaldson 2625015) de klarar den amerikanska klassningen MERV 15 (tar minst 85% av partiklar mellan 0,3 och 1 mikrometer) som Bill rekommenderar och har lite mer än 20 m2 filtermediaarea per filter, så drygt 40 m2 totalt. Gick på 3000 kr per filter ink moms från Protec filter / AirPro Filter.
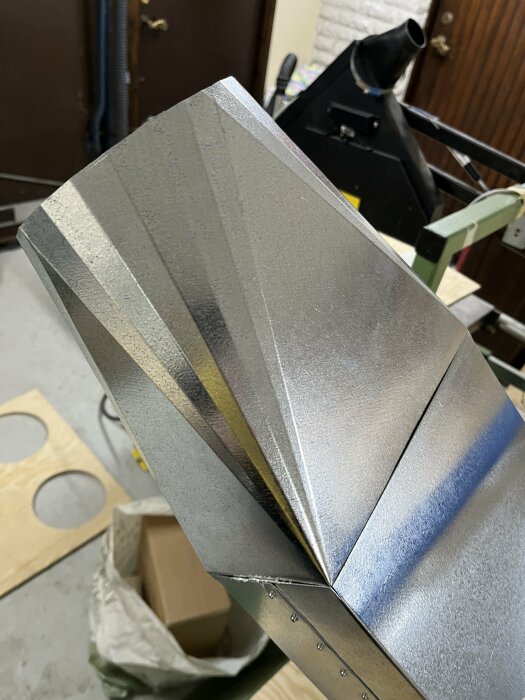
Inloggade ser högupplösta bilder
Logga in
Skapa konto
Gratis och tar endast 30 sekunder
Sedan popnita fast och täta. Har just nu en spironippel på.
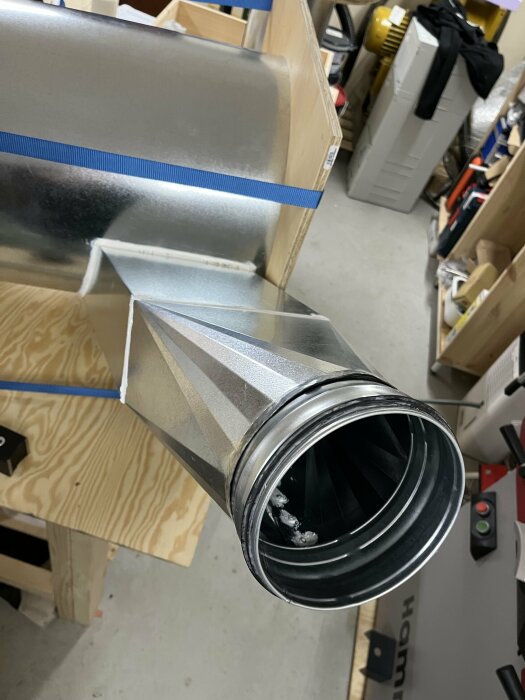
Inloggade ser högupplösta bilder
Logga in
Skapa konto
Gratis och tar endast 30 sekunder
Skruvade fast utloppsröret i plywoodlocket och plywoodlocket i cykloncylindern. Utloppscylindern tog emot lite inloppet, så möjligen skulle jag gjort utloppet någon mm mindre efter att diametern på huvudcylindern blev mindre.
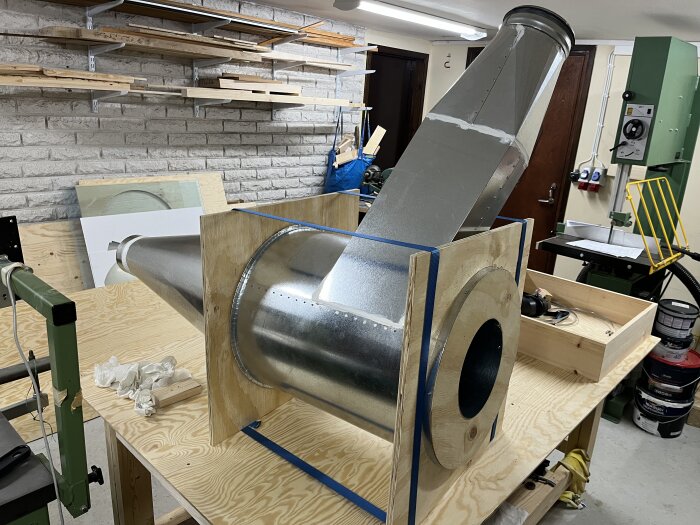
Inloggade ser högupplösta bilder
Logga in
Skapa konto
Gratis och tar endast 30 sekunder
Byggde ihop plywooden med några reglar för att kunna hänga upp den. Använde rejäla vinkelbeslag och väggkrokar för att hänga upp den. Eftersom jag endast har 2,10 m i takhöjd behöver jag sätta den vinklad. Finns en diskussion på Fine woodworking forum (tror jag att det var) där de diskuterar detta, Bill ska ha testat detta och det funkar bra så länge man har ca 30 graders lutning på konen så att större bitar glider ned.

Inloggade ser högupplösta bilder
Logga in
Skapa konto
Gratis och tar endast 30 sekunder
Filter
Som filter har jag köpt två st patronfilter (Donaldson 2625015) de klarar den amerikanska klassningen MERV 15 (tar minst 85% av partiklar mellan 0,3 och 1 mikrometer) som Bill rekommenderar och har lite mer än 20 m2 filtermediaarea per filter, så drygt 40 m2 totalt. Gick på 3000 kr per filter ink moms från Protec filter / AirPro Filter.
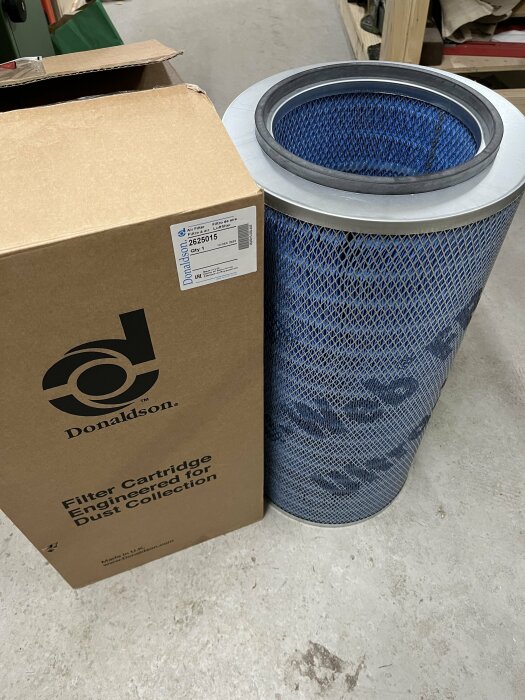
Inloggade ser högupplösta bilder
Logga in
Skapa konto
Gratis och tar endast 30 sekunder
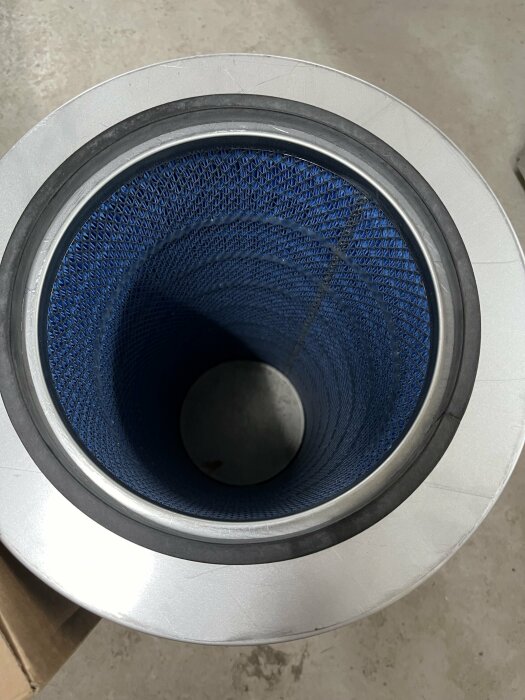
Inloggade ser högupplösta bilder
Logga in
Skapa konto
Gratis och tar endast 30 sekunder
Långsammare uppdateringar nu då jag är ikapp nutid. Gjorde en plywoodcirkel som jag limmade fast en 200 mm stos på för utloppet. Skar ut en bit gummi som packning och skruvade fast på toppen av cyklonen.
Fått hem oljefatet som ska bli uppsamlingskärl.
Sedan behövde fläkten lite kärlek. Vid utblåset saknades övergång kvadratisk till rund. Det kan jag ju nu, så gjorde en egen. Denna gång bockade jag den själv, gick rätt så smidigt faktiskt. Använde en bit vinkelprofil i stål som jag spände fast vid viklinjen, sedan böja upp genom att trycka med träbit och/eller slå med hammare direkt på.
Sedan böja sidorna, borra hål och fästa.
Framsidan på fläkten fäste jag en stos på. Klippte flärpar som kunde vikas, sedan limma fast på den befintliga.
Byggde en ställning av trä för att få upp fläkten en bit, tillräckligt för att kunna ha filtren kopplade parallellt efter.
Sammankopplade sedan med cyklonen. Har provkört och den verkar suga bra! Nästa steg blir att fixa låder till filterrens och koppla på spåntunnan. Sedan är detta i princip klart, ”bara” rördragning och utsug vid maskinerna kvar 😅
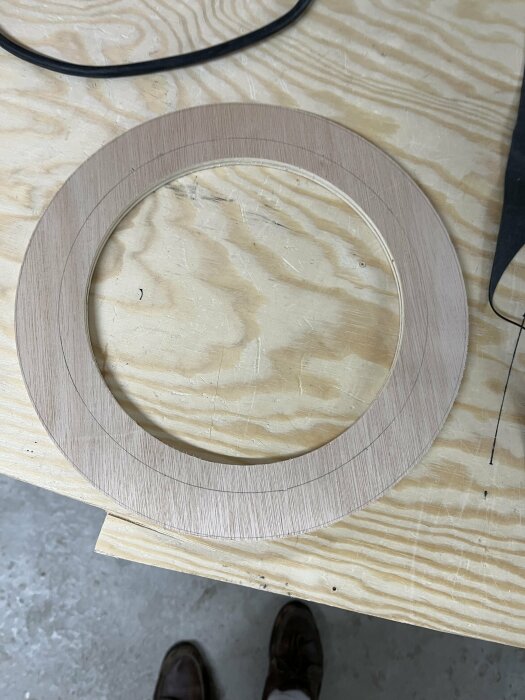
Inloggade ser högupplösta bilder
Logga in
Skapa konto
Gratis och tar endast 30 sekunder
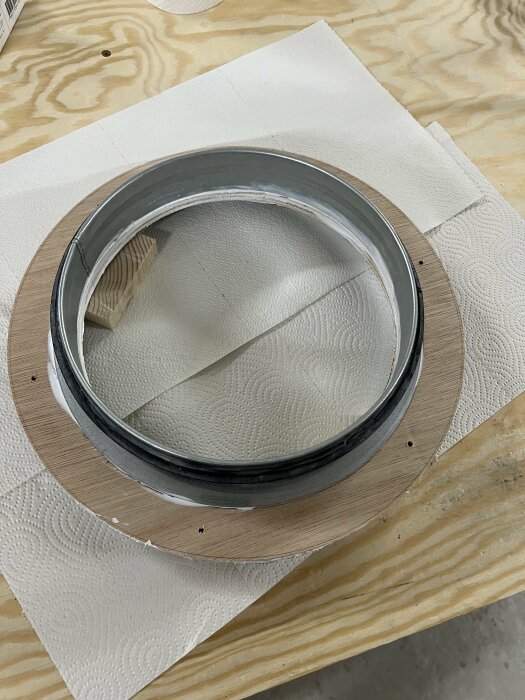
Inloggade ser högupplösta bilder
Logga in
Skapa konto
Gratis och tar endast 30 sekunder
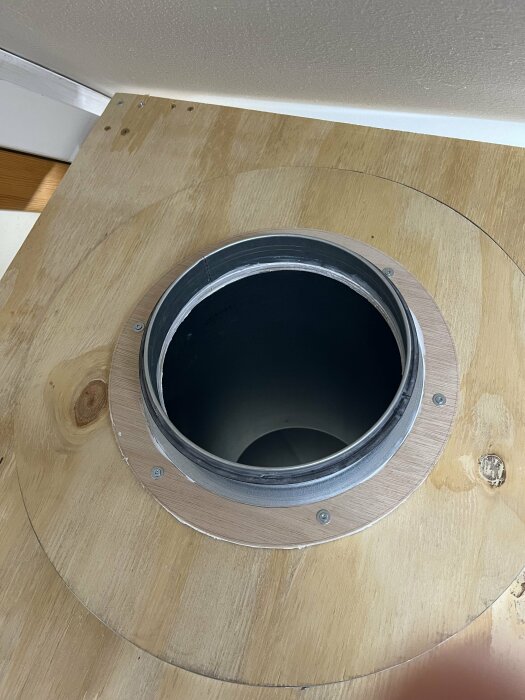
Inloggade ser högupplösta bilder
Logga in
Skapa konto
Gratis och tar endast 30 sekunder
Fått hem oljefatet som ska bli uppsamlingskärl.
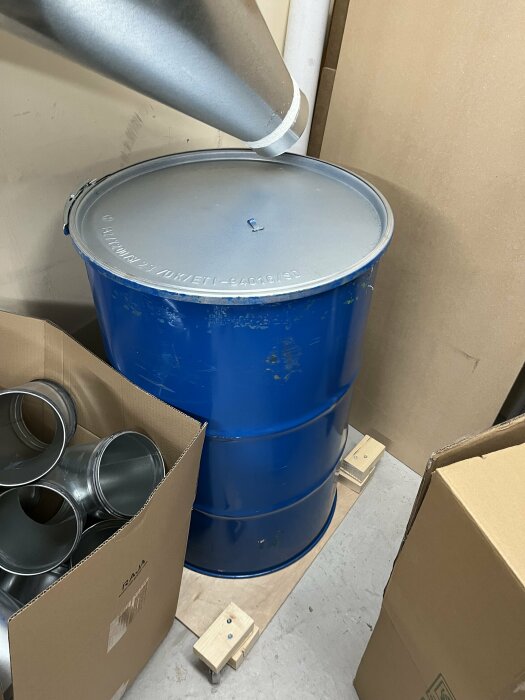
Inloggade ser högupplösta bilder
Logga in
Skapa konto
Gratis och tar endast 30 sekunder
Sedan behövde fläkten lite kärlek. Vid utblåset saknades övergång kvadratisk till rund. Det kan jag ju nu, så gjorde en egen. Denna gång bockade jag den själv, gick rätt så smidigt faktiskt. Använde en bit vinkelprofil i stål som jag spände fast vid viklinjen, sedan böja upp genom att trycka med träbit och/eller slå med hammare direkt på.
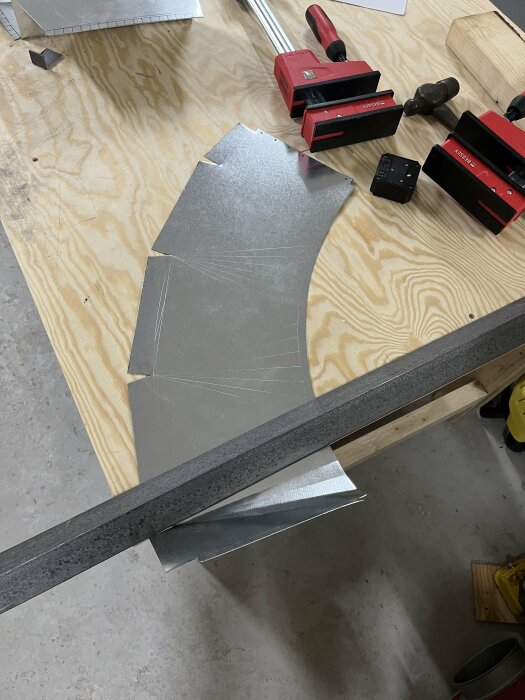
Inloggade ser högupplösta bilder
Logga in
Skapa konto
Gratis och tar endast 30 sekunder
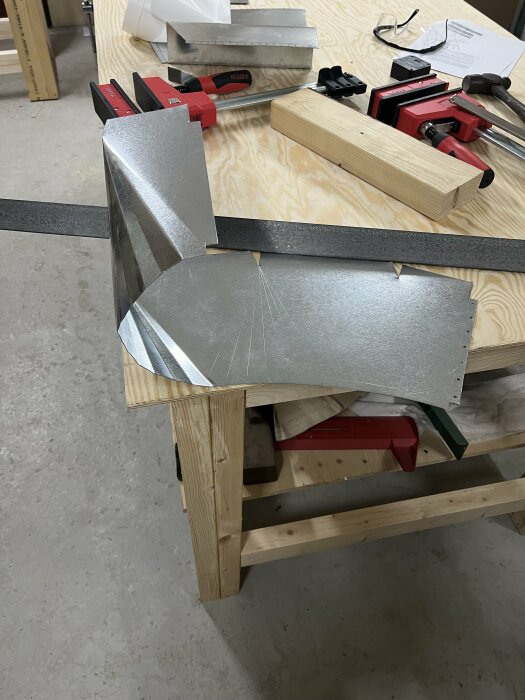
Inloggade ser högupplösta bilder
Logga in
Skapa konto
Gratis och tar endast 30 sekunder

Inloggade ser högupplösta bilder
Logga in
Skapa konto
Gratis och tar endast 30 sekunder
Sedan böja sidorna, borra hål och fästa.
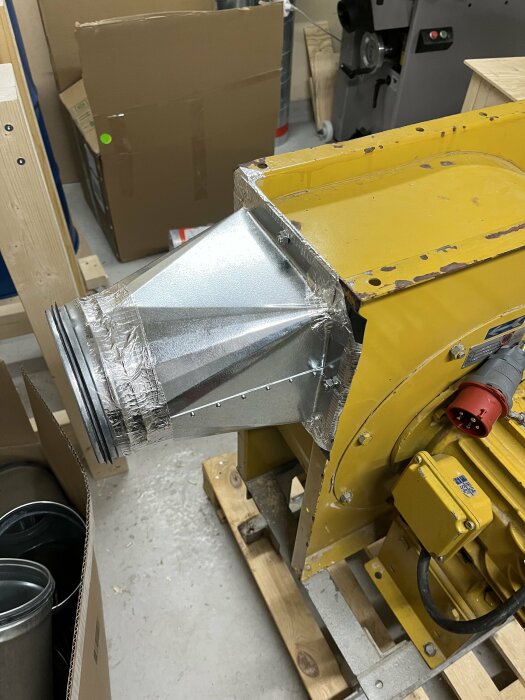
Inloggade ser högupplösta bilder
Logga in
Skapa konto
Gratis och tar endast 30 sekunder
Framsidan på fläkten fäste jag en stos på. Klippte flärpar som kunde vikas, sedan limma fast på den befintliga.
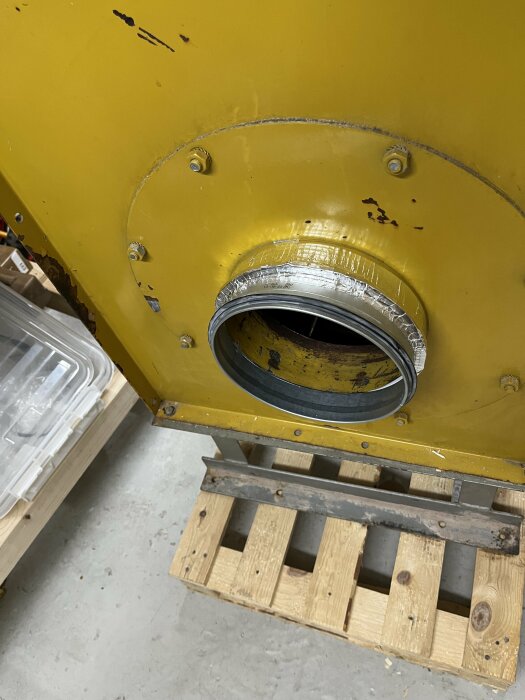
Inloggade ser högupplösta bilder
Logga in
Skapa konto
Gratis och tar endast 30 sekunder
Byggde en ställning av trä för att få upp fläkten en bit, tillräckligt för att kunna ha filtren kopplade parallellt efter.
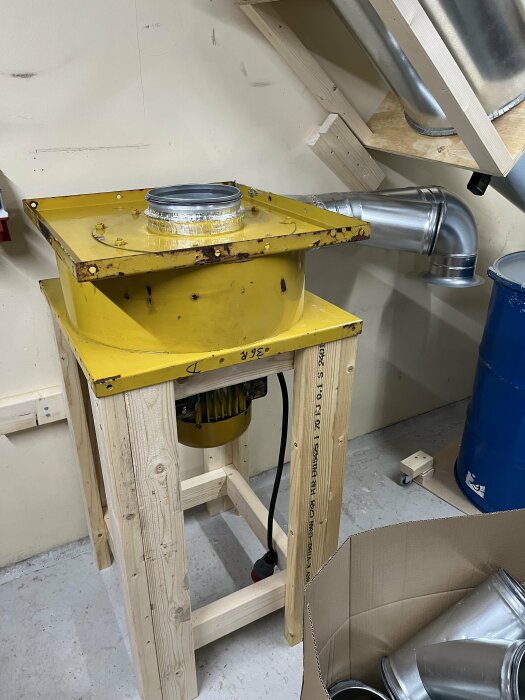
Inloggade ser högupplösta bilder
Logga in
Skapa konto
Gratis och tar endast 30 sekunder
Sammankopplade sedan med cyklonen. Har provkört och den verkar suga bra! Nästa steg blir att fixa låder till filterrens och koppla på spåntunnan. Sedan är detta i princip klart, ”bara” rördragning och utsug vid maskinerna kvar 😅
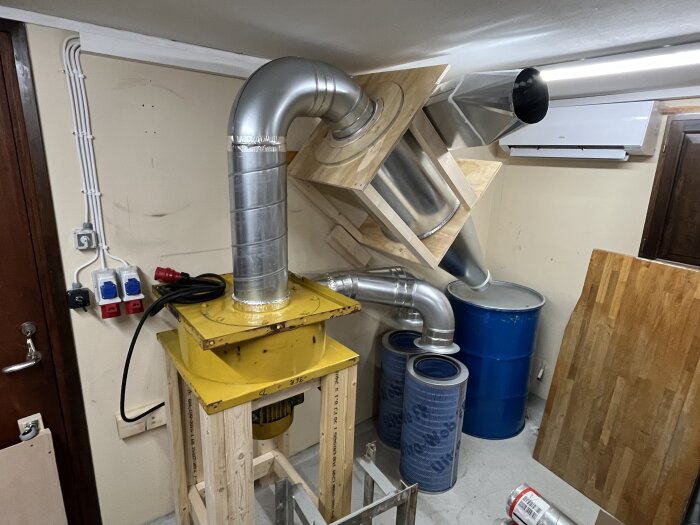
Inloggade ser högupplösta bilder
Logga in
Skapa konto
Gratis och tar endast 30 sekunder