Sveriges första 3D-printade hus - så fungerar tekniken
Ett svenskt gäng står bakom en 3D-printer tänkt att inom kort kunna skriva ut fullskaliga hus. Man har redan testat tekniken på ett 24 kvadratmeter stort hus i betong och sett att den fungerar.

Tobias von Haslingen byggde en 3D-skrivare för att skriva ut ett hus i betong tillsammans med en kompis. Foto: Privat
Resan med att ta fram en 3D-skrivare för hus började med två vänner 2015.
– Vi ville testa om man kunde skriva ut hus i 3D-skrivare. Min kompis hade byggt en 3D-skrivare för plast och vi började titta på att göra samma sak men för betong. Vi kämpade med det i några år och till slut hade vi löst alla utmaningar så att det gick att skriva ut ett helt hus, säger Tobias von Haslingen.
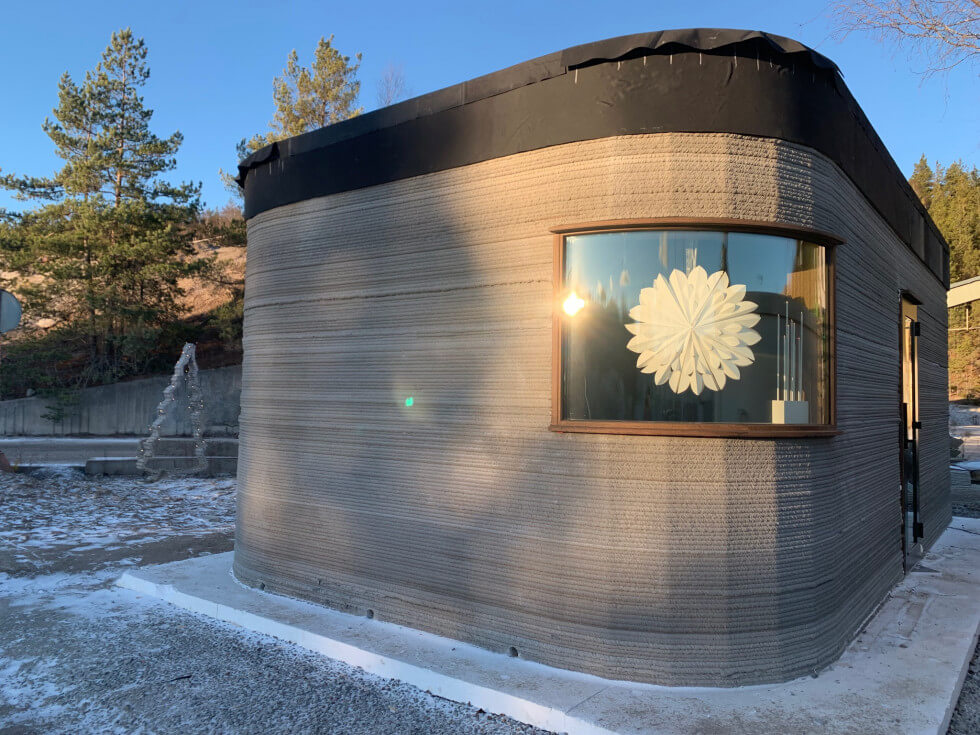
Sagt och gjort, de gjorde en testutskrift.
– Vi hade inte tänkt igenom infästningen för tak-konstruktionen helt för vi trodde faktiskt inte att det skulle gå hela vägen på första försöket. Men det gjorde det, säger Tobias.
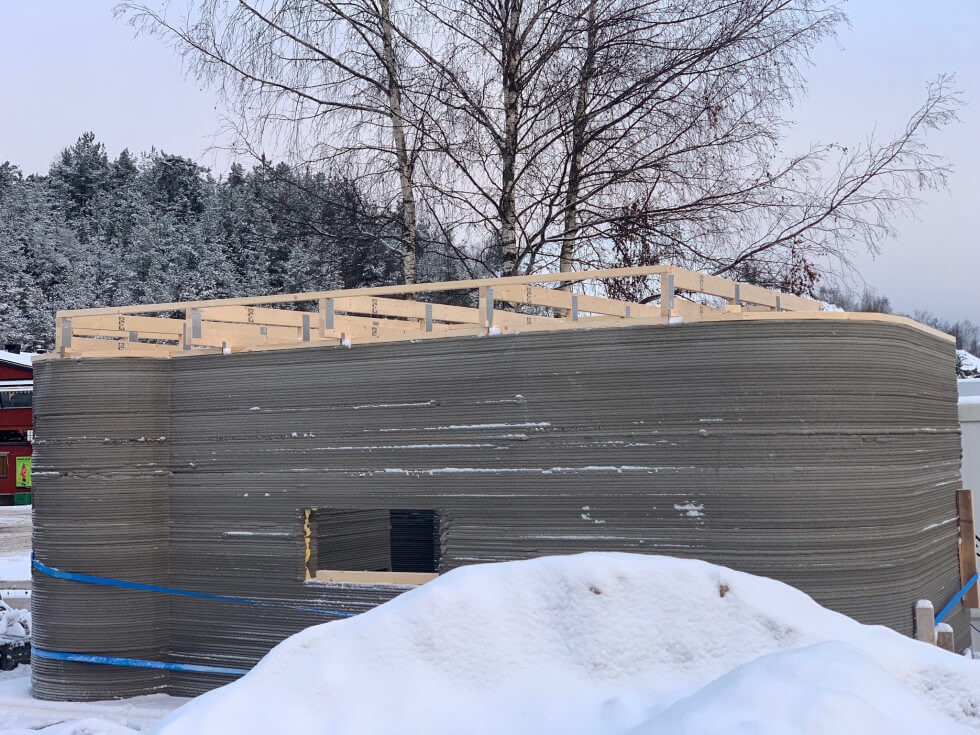
De kunde dra många lärdomar från huset och såg vad man behövde förbättra. Nu jobbar de för fullt på nästa generation av skrivaren som ska bli snabbare, ha större noggrannhet och kunna skriva ut större hus. Målsättningen med projektet är att få ner byggkostnaderna för småhus och samtidigt automatisera branschen.
– I vårt 24 kvadratmeter stora hus är materialkostnaden för stommen strax över 32 000 kronor. Det får du inte ens panelvirke för till ett vanligt hus idag. Så det är väldigt effektivt sätt att bygga på. Allt pekar på att det ska bli billigare, säger Tobias von Haslingen.
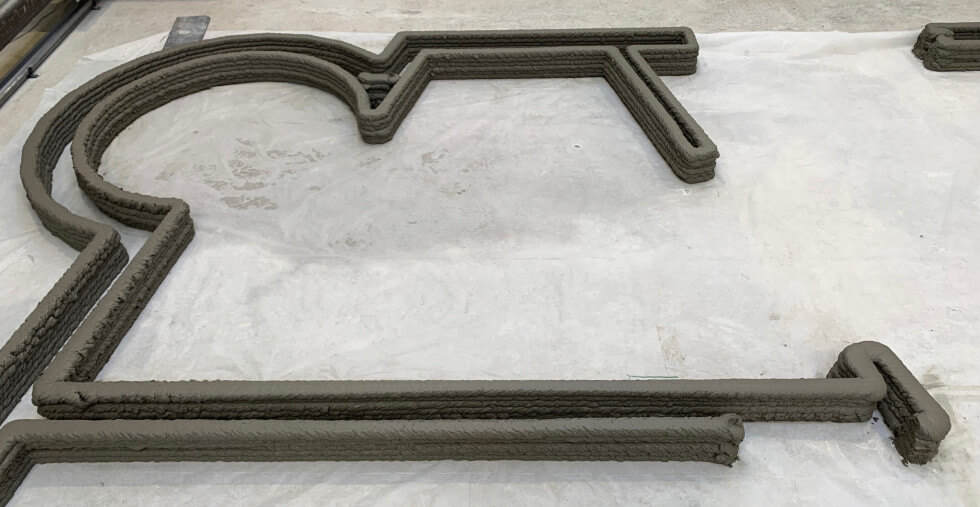
Så fungerar tekniken
Det finns två sätt att skriva ut huset på. Det ena är att man först gjuter en platta (husgrund) och därefter skriver ut huset på den plattan. Det andra alternativet - som är bäst när huset ska ha mer avancerade former såsom rundade hörn och liknande - är att man skriver ut ytterbalken också, isolerar på insidan och sedan gjuter plattan på insidan.
Det tog 28 timmar att skriva ut vårt första hus
Det tar 1-2 dagar att skriva ut en våning på drygt 100-150 kvadratmeter.
– Det tog 28 timmar att skriva ut vårt första hus, men det är för att vår prototypskrivare rör sig ganska långsamt - så blir det inte med nästa generation, den kommer att skriva ut fortare. På 48 timmar bör man kunna skriva ut en stor våning. Sedan får man gjuta ett mellanbjälklag och kan skriva ut nästa våning, säger Tobias.
Läs mer: Guide köpa 3D-skrivare och skriva ut egna saker
Med utskriften klar är det dags att borra upp hål i betongen för eldosor och eldragning. På sikt är tanken att man skriver ut huset med färdiga håligheter, men med prototypen de har idag är det bättre att använda en hålsåg.
– Antingen printar man inte där man vill ha hål, eller så borrar man ur betongen när den fortfarande är fuktig så att man får ett fint hål. Man tar en vanlig hålsåg, sågar rakt igenom och då får man ett jättefint hål som man i princip kan montera elkontakten i direkt, man behöver egentligen inga dosor. Vi har även testat renoveringsdosor, och det fungerar också utmärkt.
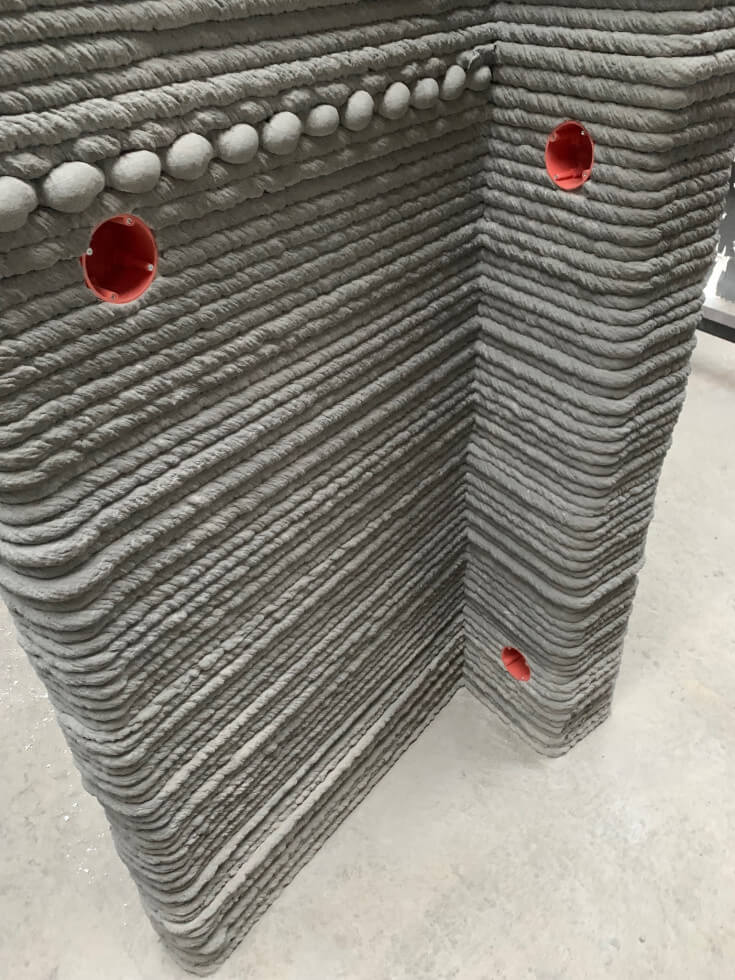
När det kommer till vattenrör är moderna rör flexibla plastslangar, och dessa får en mjuk böj vars vinkel man måste ta hänsyn till under planeringen. Hur man gör under utskriften varierar. Här finns två alternativ, det ena är att någon lägger dit dem under printmomentet, det andra är att man har en vägg med distans så man kan dra rören i efterhand.
Det är under dessa två moment som fördelen med 3D-skrivare blir lite extra tydlig. Kostnaderna för elektriker och rörmokare minskar drastiskt. Under ett projekt i Tyskland halverades tiden som man behövde ha elektriker på plats, eftersom allt var så välplanerat från början så minskade arbetstimmarna avsevärt.
– Forskningen som finns internationellt sett pekar på att 3D-skrivare kan minska byggkostnaden med 70 procent. Jag skulle inte våga gå så långt. Vi tror att man kan nå en 30-procentig reduktion på huspriset, men då måste saker vara mer färdigt, säger Tobias och syftar på att de fortfarande har en del utmaningar att lösa med sin skrivare.
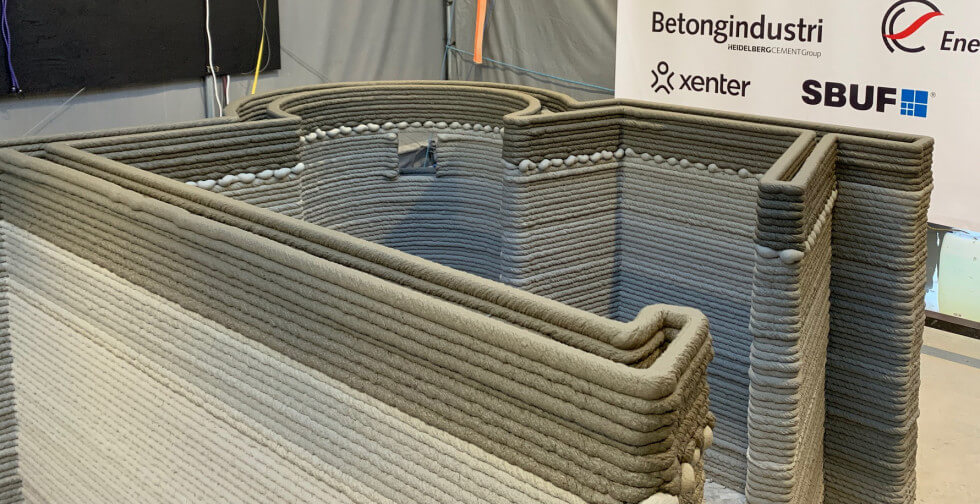
Med rör och el på plats är det dags att isolera. Valen står idag mellan polyuretanskum, frigolitkulor, gullfiber eller stenull. Tobias säger att ekofiber i dagsläget går bort då det finns risk för låg isoleringsgrad om det blir ett hål i betongväggen och det organiska materialet kommer då att förstöras. För att komma runt detta har man kontakt med en professor på KTH och tittar på olika typer av lösningar.
Valet av isolering och isolationsvärde påverkar väggarnas tjocklek, och beror även på vilken energiklass man vill uppnå.
– Vi har tittat på att göra 45 centimeter tjocka väggar med speciell utformning, man har stöd mellan väggarna. Man bygger upp det som ett fackverk och det blir oerhört mycket plats för isolering, säger Tobias von Haslingen.
Sedan bygger man tak och sätter in fönster. I det 24 kvadratmeter stora huset som man redan har printat sitter det fönster- och dörrkarmar som är 3D-printade, men då av deras samarbetspartner Nordan.
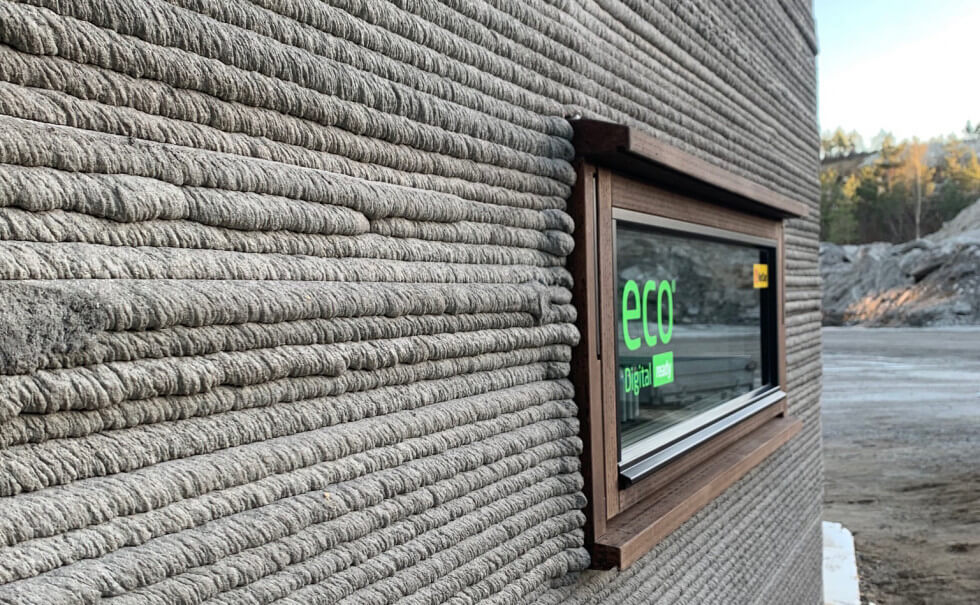
– De fönster vi har utvecklat med Nordan har lite speciella egenskaper, så man kan dra ner toleransen, man behöver inte ha en centimeter glipa runtom karmen. Vi ville komma ner så man bara behöver sätta en elastisk fog runt fönstren, säger Tobias och fortsätter:
– Vi har lite problem med noggrannheten när man startar och stoppar printern, så då skar vi en jämn kant, men på sikt kommer det vara helt jämnt.
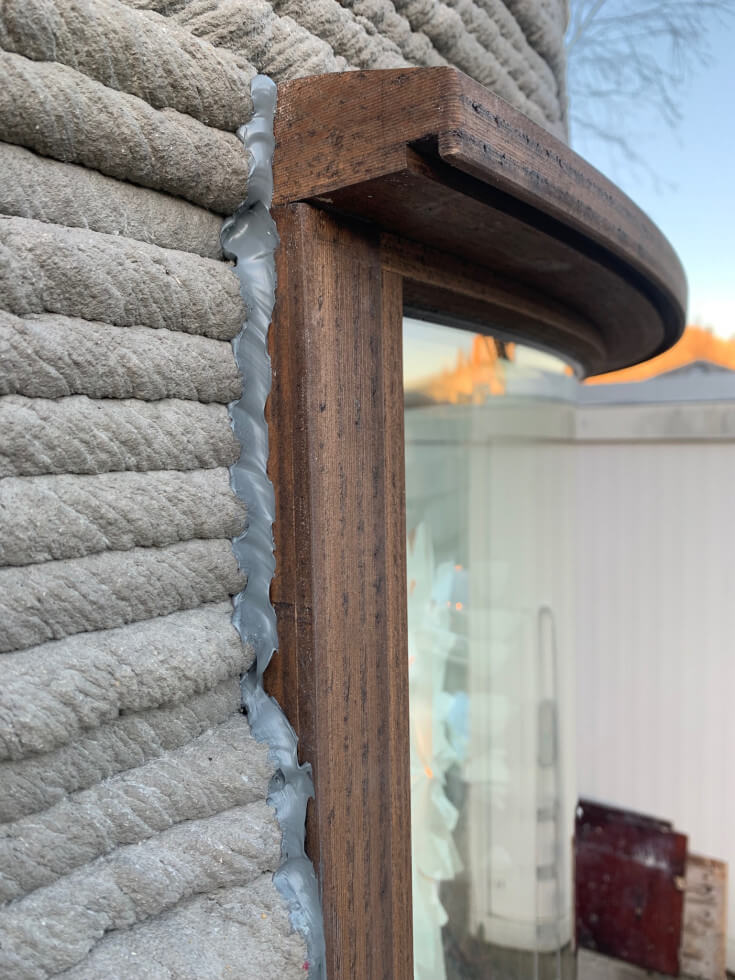
Taket beror på vilken typ av takkonstruktion man valt. Vanligt A-tak blir traditionella takstolar, men ska man göra pulpettak kommer man vilja printa en kröningsmur eftersom du behöver få till infästningsgspunkter i taket på något vis.
– Vi har provat en teknik där vi använde hammarband och lade taket ovanpå, men vi trodde inte att vi skulle lyckas hela vägen första vändan så vi hade inte tänkt igenom det ordentligt. På sikt kommer vi nog hitta andra lösningar, när vi får tänka efter lite mer, säger Tobias.
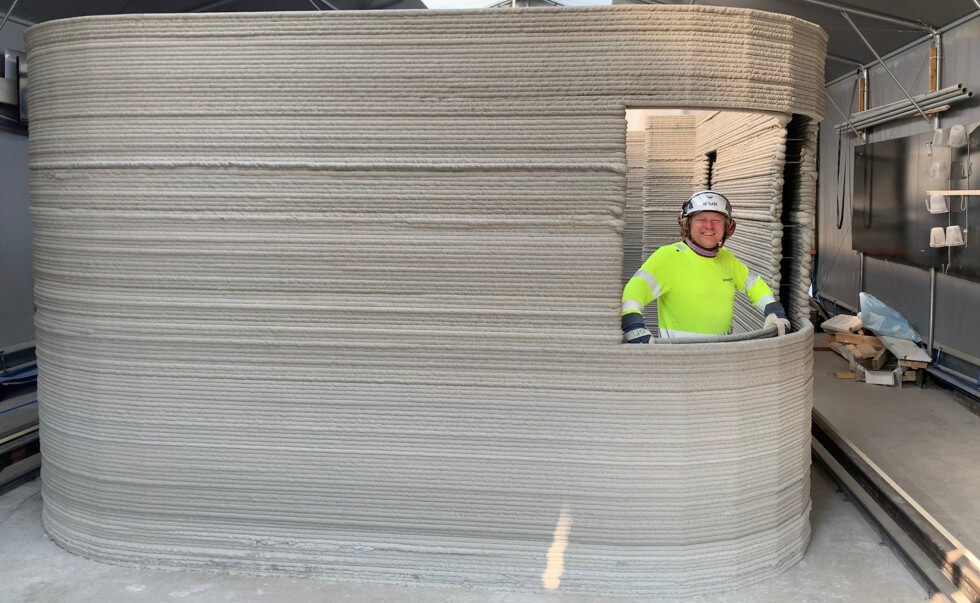
Utvecklat egen betong
Det finns många utmaningar när man skriver ut ett hus med hjälp av en 3D-skrivare. En sådan utmaning är betongen. Dels ska den vara mjuk nog att kunna pumpas ut, men samtidigt hållfast nog för att behålla formen även när det blir tryck ovanifrån. Sedan ska den ha en öppentid så att nästa lager binder med föregående lager.
Tobias och hans kollega har utvecklat en egen betong för ändamålet. Man tittar även på att ta fram en ekobetong.
– Nästa steg är att göra den mer cirkulär. En hög hållfasthetbetong är ett sådant projekt så man kan gå ner i mängden betong som krävs, ett annat projekt är att göra samma sak fast med ekologiska aspekter såsom att blanda in återvunnen betong.
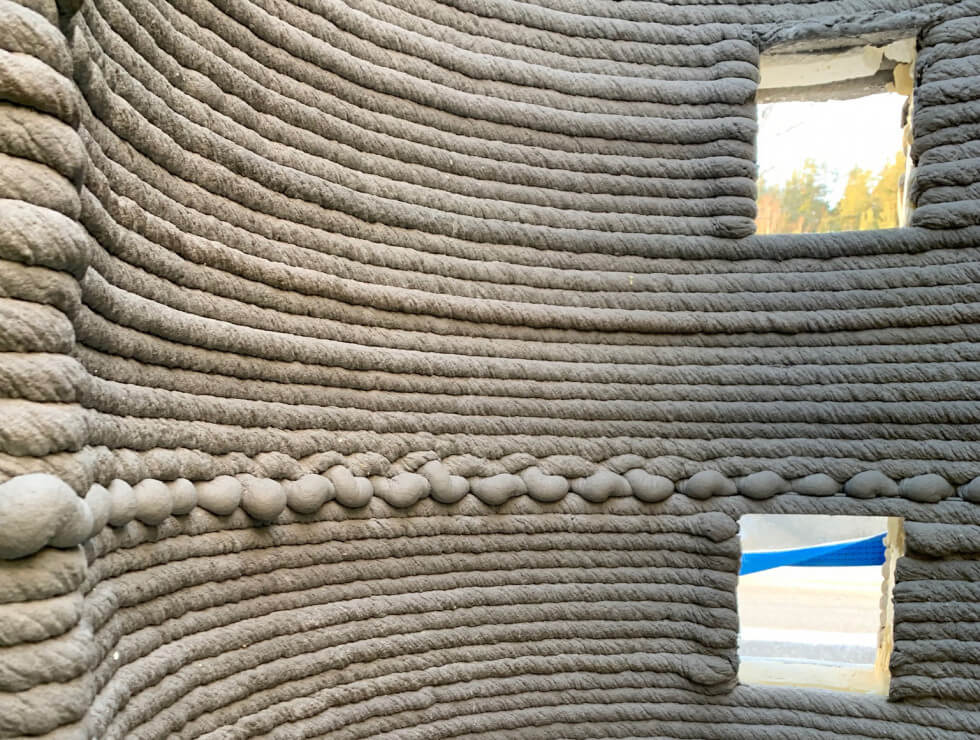
Utöver att arbeta på betongen så har man förstås även nästa generation skrivare som man fokuserar mycket på. Den är modulär. Tanken är att man ute på byggplatsen ska kunna bygga ihop den på två timmar, och att det inte ska kräva mer än två personer.
Fullt utbyggd är den här nya generationen skrivare 20 meter lång. Men den har en räls så i praktiken kan du förlänga den oändligt. I övrigt blir den 15 meter bred och 10 meter hög.
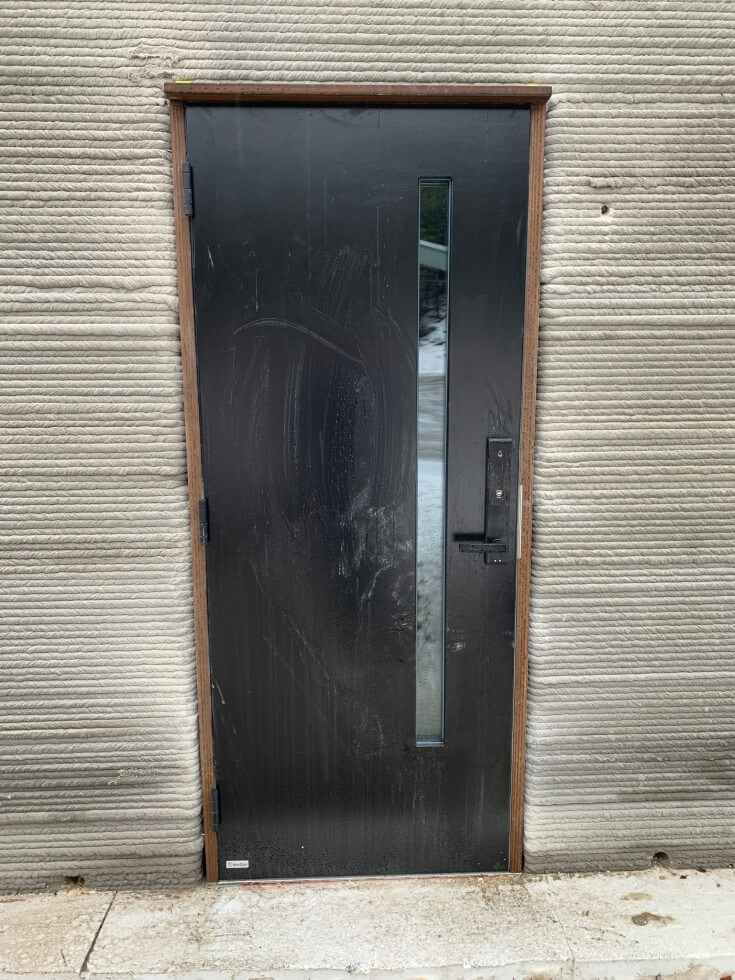
De arbetar just nu på kalibreringen.
– Det är en del elektronikjusteringar som måste göras för att den ska kunna kalibrera sig själv på plats. Det är mer produktionsteknik vi är inne och tummar på.
Varför gör då Tobias och hans kollega detta projekt?
– Vi vill sälja 3D-printmöjligheter men det är lite svårt om man inte kan visa att det fungerar. Sedan är det dyrt att utveckla sådana här skrivare. Så vi försöker skapa en marknad samtidigt som vi utvecklar 3D-tekniken.
De söker finansiärer och samarbetspartners som kan arbeta tillsammans med dem för att förfina och förbättra tekniken. Finansiärer behövs för att de ska ha råd med allt. I år ska de exempelvis köpa loss en tomt till det nya huset som ska skrivas ut. De är även mitt i ansökningsprocesser om att få genomföra större forskningsprojekt. Det är många bollar i luften samtidigt.
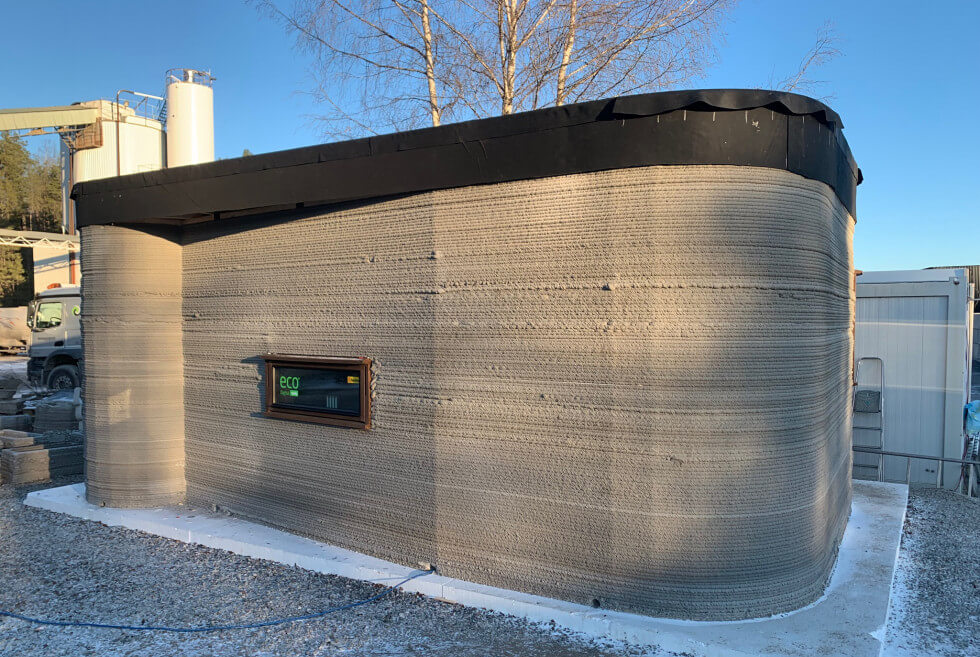
– Målet är en fullskalig husmodell som vi på sikt tänkt sälja och därmed se till att vi får ett första 3D-printat hus i Sverige där någon bor dagligdags. Men för att nå dit är det mycket som ska falla på plats.
Det långsiktiga målet är dock att minska byggkostnaderna.
– Vi behöver få ner byggkostnaderna så att fler har råd att bygga och bo i hus, avslutar Tobias. Jag tror att detta är rätt väg att gå.
Kommentarer
103